Статья впервые опубликована в сети 19 мая 2009 года, а также в №4, 2009 журнала «Пластикс» / Обновлена 22 февраля 2021 года
Представьте, что перед вами стоит задача получить ударопрочную, кристально прозрачную с глянцем ёмкость с ручкой сложного дизайна объёмом не менее 1–2 литров для упаковки продукта, чувствительного к внешней среде.
- Стандартный ПЭТ не подойдёт, т.к. возникнут проблемы с ручкой и распределением массы из-за сложного дизайна и мелких деталей.
- Полипропилен не подойдёт, т.к. не обеспечит полную кристальную прозрачность даже с «осветлителями».
- ПВХ вряд ли подойдёт, т.к. поиск поставщиков выдувного ПВХ и утилизация готовых изделий из него становится всё сложнее.
- ПЭТГ не подойдёт, т.к. из-за текучести рукава из него очень сложно выдувать изделия больше 100 мл.
- Поликарбонат также не подойдёт из-за сложностей переработки и чересчур высокой себестоимости изделий.
- Наконец, полистирол не подойдёт из-за низких барьерных свойств и хрупкости.
Задачу решает сополиэфир Aspira EB062 от компании Eastman, который фактически является ПЭТом, пригодным для экструзионно-выдувного формования. Таким образом, разрушается выстраиваемая десятилетиями стена, разделяющая два метода получения выдувных изделий – из ПЭТ через стадию преформ, и из полиолефинов и группы альтернативных материалов через рукав экструзионно-выдувным формованием. ПЭТ Aspira отличается прекрасными барьерными свойствами (в т.ч. по спиртосодержащим), прекрасным внешним видом и, главное, хорошей ударопрочностью и жёсткостью, что позволяет без проблем производить из него и крупногабаритную тару – 5, 10, 20 литров и более.
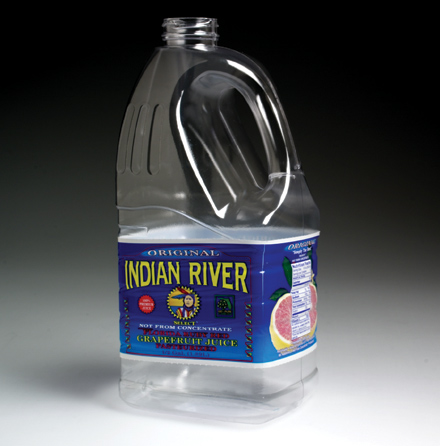
Разработки и практический выпуск для рынка марок ПЭТ, пригодных для экструзионно-выдувного формования на самом деле ведётся компанией Eastman уже более 25 лет, хотя мало кто из российских переработчиков об этом знает. Марка EB062 является своего рода венцом усилий Eastman в этой области и объединила в себе несколько ключевых свойств:
- Кристальная прозрачность с глянцевой поверхностью
- Отличные барьерные свойства и химическая стойкость
- Жёсткость и ударопрочность
- Лёгкость переработки
- «Экологичность» и простота утилизации
Преимущества материала открывают новые способы его применения в различных отраслях.
Применения
Упаковка для напитков
Из сополиэфира ПЭТ можно производить уникальные по внешнему виду бутылки для сока и других напитков. Это могут быть большие бутылки объёмом 2 литра с элегантной ручкой и дизайном, который ограничивается только вашей фантазией. Любые мелкие детали, изгибы, сечения – всё это возможно, благодаря гибкому распределению массы, обеспечиваемому экструзионно-выдувным формованием.
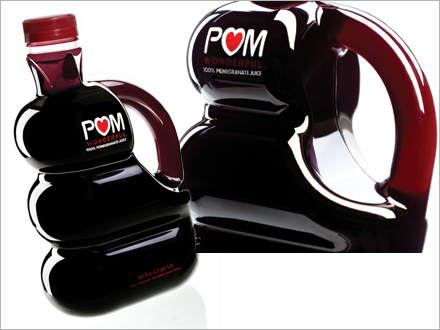
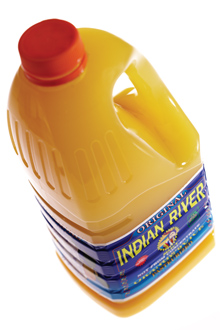
На российском рынке сокосодержащих напитков вообще наблюдается дефицит хорошей упаковки 2-3-х литрового класса. Картонная упаковка неудобна в использовании и непрозрачна, а классическая круглая ПЭТ-бутылка также не очень удобна из-за отсутствия ручки и визуально не выделяется на прилавке из-за сходства с бутылками для воды и газированных напитков. 3-х литровые стеклянные банки с жестяной крышкой выглядят архаично, а в удобстве использования вообще не выдерживают никакой критики. 1-2-3-х литровая бутылка с ручкой – прекрасный способ дифференцирования вашего продукта и придания ему премиального имиджа. Производители в США уже поняли это, и сейчас сок в уникальных ПЭТ-бутылках с ручками прекрасно продаётся.
19-литровые бутыли для воды и другие ёмкости из поликарбоната
Бутылки многоразового использования наивысшего качества производят из поликарбоната. Именно поликарбонат традиционно обеспечивал необходимый комплект свойств для этого изделия – прозрачность, прочность и возможность экструзионно-выдувного формования с ручкой. Из поликарбоната экструзионно-выдувным методом изготавливают 19-литровые бутыли крупнейшие производители этих ёмкостей в России.
Однако, заключения американских учёных выявили возможность чрезмерного остаточного наличия в поликарбонате вещества Бифенол А (бифенол А является одним из исходных компонентов для производства поликарбоната). Бифенол А может оказывать вредное воздействие на здоровье человека и, в частности, вызывать рак. По этой причине от поликарбоната стали отказываться многие наиболее ответственные европейские и американские производители упаковочных ёмкостей из поликарбоната, имеющих пищевое и/или медицинское применение.
Новый сополиэфир ПЭТ может полноценно заменить поликарбонат в сфере производства 19-литровых бутылей и других родственных ёмкостей, т.к. обладает отличной прочностью, прозрачен и перерабатывается экструзионно-выдувным формованием. При этом он абсолютно безвреден для здоровья.
Косметические флаконы преимум-класса
Косметические флаконы премиум-класса нестандартного дизайна с помощью ПЭТа Aspira можно производить без ограничений. Этот материал одновременно позволяет иметь:
- Острые углы, мелкие острые элементы и такие детали, как мини-ручки и подвесные крюки на дне.
- Яркий глянцевый блеск и кристальную прозрачность.
- Размер флакона более 200 мл.
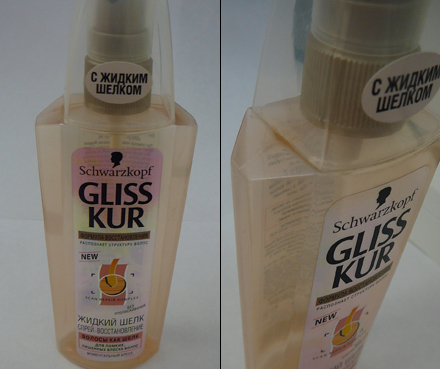
Ни один из альтернативных видов экструзионно-выдувного сырья (ПЭТГ, ПВХ, ПС и т.п.), так же как и классический выдув ПЭТ из преформ, не позволит достичь всех этих свойств одновременно.
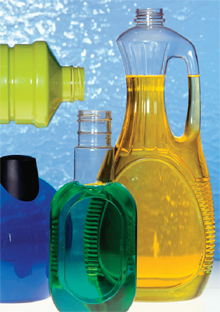
Упаковка для моторных масел и автокосметики
Полностью прозрачные канистры с ручкой объёмом 3-10 литров – необычное, а значит привлекательное и выделяющееся решение для упаковки дорогих видов моторных масел и смазок, а также автомобильных моющих, чистящих средств и другой автокосметики. Подобную упаковку уже используют некоторые производители смазочных материалов в США.
В России и странах СНГ прозрачные канистры хорошего качества абсолютно отсутствуют на прилавках, что позволит первой компании, применившей подобную упаковку, заметно дифференцироваться.
Переработка
В целом, переработка сополиэфира ПЭТ экструзионно-выдувным формованием, конечно, несколько сложнее, чем переработка классического полиэтилена, но при соблюдении правильной технологии процесс является вполне доступным.
Подготовка материала
Так же как и классический ПЭТ, аморфный сополиэфир Eastar требует тщательной просушки. Наиболее рекомендуемым (и фактически единственным) способом её осуществления является использование влагоустраняющих устройств с силикагельными ситами. Такие влагоустранители позволяют стабильно и равномерно осуществлять просушку сырья до необходимой глубины.
Стандартные параметры сушки сополиэфира ПЭТ подразумевают температуру циркулирующего воздуха 65 градусов по Цельсию и 6-часовой процесс до содержания влаги на уровне 0,05%. Такие параметры, как размер сушильного бункера, мощность самого влагоустранителя и количество силикагельных сит должны быть согласованы между собой и обычно рассчитываются поставщиком осушающей системы. Для расчёта достаточно знать количество предполагаемого к переработке сырья в час.
Экономить на системе сушки, или каким-то ещё образом пренебрегать технологией на этом этапе не следует, т.к. качество сушки напрямую влияет на качество конечного изделия и стабильность всего экструзионно-выдувного процесса.
Экструдер
Шнек для переработки сополиэфира ПЭТ должен иметь профиль, создающий малые сдвиговые усилия для предотвращения перегрева и термодеструкции материала. Стандартные шнеки, оптимизированные для полиэтилена низкого давления, при работе с сополиэфиром генерируют слишком «сильный» расплав и разрушают материал. Кроме того, полиэтиленовые шнеки, как правило, оснащены смесительными секциями, которые также способствуют перегоранию сополиэфира, при том, что в таких смесительных секциях нет технологической необходимости при переработке прозрачных материалов. Переработка ПЭТ на полиэтиленовых шнеках допускается только при небольшой производительности и/или коротких рукавах.
Ствол экструдера при переработке сополиэфира ПЭТ требует кондиционирования. Его можно осуществлять либо посредством простых вентиляторов на каждой из температурных зон, либо с помощью масляной рубашки с регулируемой температурой. Решение с масляной рубашкой, также рекомендуемое при переработке ПВХ, является более предпочтительным, т.к. общий технологический процесс становится более контролируемым. При применении масляной рубашки её температура обычно поддерживается на уровне 120 градусов по Цельсию. Дополнительный контур охлаждения, проходящий внутри шнека, который часто применяют для выдува из ПВХ, для сополифира использовать не только не обязательно, но и вредно, т.к. это может вызвать застывание фрагментов материала в зоне загрузки.
Практика показала, что экструзионно-выдувные машины, сконфигурированные для переработки ПВХ или поликарбоната, хорошо подходят и для работы с ПЭТ сополиэфирами семейства Aspira.
Температуры на зонах при переработке сополиэфира могут варьироваться в диапазоне 190–230 градусов по Цельсию. Конкретный профиль температур зависит от особенностей конкретного технологического процесса. Возможны профили как с понижением температуры от зоны загрузки к нижней зоне головки, так и с повышением. Так же для преодоления трудностей с загрузкой и/или предотвращения чрезмерной механической нагрузки на экструзионную головку возможна работа на повышенных температурах изначально с последующим их уменьшением при стабилизации процесса.
Экструзионная головка
Для переработки сополиэфира ПЭТ оптимально подходят прямоточные экструзионные головки торпедного типа (с равномерным растеканием потока вокруг центральной конусообразной торпеды, а не рассечением на части). Такие торпедные головки со сглаженным дизайном без застойных зон из хромированной и/или нержавеющей инструментальной стали используются и для ПВХ. Сополиэфир Aspira также успешно перерабатывается через аккумуляторные (накопительные) экструзионные головки, что позволяет производить ёмкости объёмом более 20 литров, весом более 1 кг и без ограничений по максимальному размеру.
Важно, чтобы экструзионная головка обеспечивала достаточный прогрев переходной зоны. В противном случае существует риск образования застывших фрагментов материала, которые нарушают целостность рукава и генерируют лишнее давление в головке.
Прессформа
Изделия из сополиэфира ПЭТ очень восприимчивы к обработке поверхности прессформы. Часто встречающаяся блестящая полированная поверхность обеспечивает глянцевую гладкую прозрачность выдувным ёмкостям, а различные шагреневые виды обработки передаются на поверхность бутылок соответствующими текстурными эффектами.
Проектирование прессформ для изделий из сополиэфира, в целом, не предполагает принципиальных особенностей, по сравнению с оснасткой для полиолефиновых материалов. Могут быть использованы те же материалы: сталь, алюминий и элементы из бериллиевой бронзы для наиболее эффективного теплообмена в критических зонах (горловина, дно, ручка).
Оптимальная температура прессформы в процессе производственного цикла – 10 градусов по Цельсию.
Использование дроблёнки
Несмотря на кажущуюся чрезмерную чувствительность процесса производства изделий из сополиэфира ПЭТ, включение в процесс дроблёного материала происходит безболезненно. Обычные для экструзионно-выдувного формования 20–40% облоя можно полностью измельчать и добавлять к первичному материалу. Можно не опасаться за потерю стабильности, внешних и прочностных свойств изделия, если дроблёнка до попадания в экструдер не была загрязнена пылью, маслом и другими веществами. Если организован автоматический процесс измельчения, транспортировки, хранения и подмешивания вторичного материала, то, как правило, проблем и не возникает.
Резюме
Инновационные свойства и возможные применения сополиэфира ПЭТ Aspira, казалось бы, вершат революцию в выдувном формовании. Маркетинговые преимущества, в частности преимущества экструзионно-выдувной упаковки для соков из ПЭТ, настолько очевидны, что даже удивительно, что ни одна из компаний из России или СНГ до сих пор её не использует.
Впрочем, технология производства этого сополиэфира действительно эксклюзивна (фактически подвластна только одной компании – Eastman), поэтому наивно ожидать, что цена на материал будет иметь «массовый» уровень. Это сырьё относится к классу дорогостоящих, и в ближайшие годы картина вряд ли изменится. Предшественник сополиэфира – ПЭТГ, пусть и производится крупными центрами (тем же Eastman, а также корейским концерном Sky), но так и не перерос статус специального материала для нишевых задач.
Сегодня и завтра сополиэфиры Eastman едва ли могут конкурировать с классическим ПЭТ по объёмам потребления, но способны выручить там, где ни обычный ПЭТ, ни другие материалы помочь не смогут.