Статья впервые опубликована в сети 26 июня 2005 года / Обновлена и переработана 19 февраля 2021 года
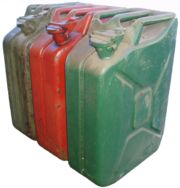
По материалам Wikipedia.org:
Кани́стра — ёмкость для топлива, сделанная из штампованной стали.
Канистра была изобретена немцами в процессе секретного проекта по заказу Гитлера. Немцы назвали ее Wehrmachtskanister. Немцы имели тысячи канистр к 1939 в ожидании начала войны.
Сегодня канистры используются для хранения топлива и воды, некоторые изготавливаются из пластмассы. Конструкция современных канистр обычно повторяет оригинальную немецкую стальную конструкцию.
Возможность изготовления пластиковых канистр с ручкой — одно из главных достоинств и применений экструзионно-выдувного формования. Пластиковые канистры применяются для фасовки и хранения технических масел, строительной, промышленной, сельскохозяйственной, бытовой и автомобильной химии, пищевых продуктов и других жидких веществ. Под канистрами прежде всего понимается полимерная тара с ручкой объёмом от 4 до 30 литров, хотя ёмкости 1–3 литра и ёмкости 40–50 литров также можно отнести к категории канистр.
Однослойные канистры, как правило, выпускаются из выдувных марок полиэтилена высокой плотности (HDPE / ПЭНД), однако для крупных видов также используют полиэтилен высокой молекулярной массы (HMWPE), который, впрочем, совершенно не популярен в России и СНГ для экструзионного выдува. Многослойные канистры применяются для агрессивных удобрений (а также некоторых других химикатов), а также для хранения топлива.
К технологическим нюансам, присущим всем видами канистр, можно отнести несколько факторов и все они являются звеньями одной цепи:
- Широкий экструзионный рукав, соответствующий по ширине конечной форме канистры
- Большое количество технологического облоя в разных областях изделия (над горловиной, на плечах и всей верхней части, под ручкой/ручками, на дне)
- Обширные зоны пережатия пластика при смыкании
- Высокие требования по усилию смыкания (не менее 80–90 кН для выдува канистры 5 литров на одном гнезде)
Подробно об особенностях изготовления канистр лучше говорить на примере их конкретных видов, поэтому прежде всего необходимо их классифицировать. В нашем понимании, нынешний рынок выделяет следующие два основных типа пластиковых канистр: канистры индивидуального дизайна и промышленные канистры широкого назначения; причём этот второй тип можно разделить на несколько категорий.
1. Канистры индивидуального дизайна
К этому типу относятся упаковочные канистры для потребительских товаров, которые одновременно имеют достаточно высокую добавленную стоимость и участвуют в жесточайшей конкурентной борьбе. Среди таких товаров: моторное масло, автокосметика и, реже, упаковка для другой потребительской продукции.
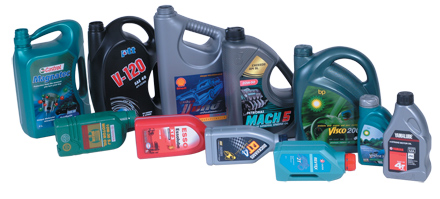
Дизайн канистры обычно есть результат долгосрочной маркетинговой работы заказчика. В крупных компаниях, как правило, сначала появляется дизайн канистры, а уже затем проверяется то, насколько хорошо он соответствует технологии экструзионно-выдувного процесса. За усложнением дизайна часто следует увеличение веса канистры и увеличение площади облойных зон, а значит себестоимости её производства. Количество облоя на некоторых канистрах для смазочных масел (например, на канистрe MACH 5 на фото) может достигать 40–50%.
Агенства, которым поручают разработку дизайна канистры и приведение его в соответствии с маркетинговым и эмоциональным наполнением торговой марки, не разбираются в экструзионно-выдувном формовании. С другой стороны — профессиональные в выдувном формовании инженеры-проектировщики обычно не сильны с креативной, художественной точки зрения. Разработчиков, объединяющих обе возможности, найти не так просто (в России по изделиям 5–10 литров и более их вообще не отыскать). Поэтому разработка хорошей канистры для потребительского товара это сложный процесс, объединяющий усилия разных категорий специалистов. Что касается наших возможностей, то компания Zabelin оказывает полную консультационную поддержку тех своих клиентов, перед которыми стоит задача разработки дизайна канистры с нуля или со стартовых эскизов. Мы помогаем проектировщикам и участвуем в процессе создания дизайна от и до, что в итоге позволяет на выходе иметь канистру хорошую не только с маркетинговой, но и с инженерной точки зрения.
Наиболее популярный типоразмер канистр индивидуального дизайна 4, 5 литров. Типовые производственные решения для этих изделий можно вывести в следующую сводную таблицу:
Гнёздность | 1 | 1 + 1 | 2 | 2 + 2 | 3 + 3 |
Кол-во станций | 1 | 2 | 1 | 2 | 2 |
Кол-во ручьёв | 1 | 1 | 2 | 2 | 3 |
Производительность в час, шт. | 150 | 300 | 300 | 600 | 900 |
Производительность в месяц (около 660 часов), шт. | 100 000 | 200 000 | 200 000 | 400 000 | 600 000 |
Примечание: Варианты рассчитаны исходя из времени цикла одной станции 25 секунд. Данное время цикла является нормальным для канистр 4-5 л весом 220-270 г, хотя, конечно, может быть как больше так и меньше в зависимости от дизайна конкретного изделия и требований к нему и в зависимости от качества охлаждения.
Инвестиции в двухстанционные машины обычно на 30-50% больше, чем в одностанционные, но разница в производительности составляет два раза. Таким образом, двухстанционные машины всегда более экономически эффективны в долгосрочной перпективе, но при выборе следует также принимать во внимание увеличивающееся в полтора-два раза время на обслуживание машины, смену форм и настройку машины.
Общее стремление любого владельца выдувной техники — снизить количество переналадок с одного изделия на другое, а в идеале работать вообще без смены прессформ (не бесконечно, но по крайней мере продолжительное время). Это стремление особенно актуально для производства канистр 4–5 литров, где большие прессформы, сложный профиль стенки и множество технологических нюансов делают смену прессформ и переналадку машины ещё более кропотливым и затратным по времени (а значит и по деньгам) занятием. Именно поэтому, если вами планируется производство канистр разных видов (например, несколько брэндов разного дизайна или канистры разного объёма, например, 4 и 5 литров), то зачастую лучше использовать две одностанционные машины нежели одну двухстанционную, несмотря на меньшие капитальные инвестиции во второй вариант.
Из опций, полезных в производстве «дизайнерских» канистр, можно выледить следующие:
- Резку рукава с запайкой и предварительным раздувом для придания рукаву широкой формы ещё до смыкания
- Возможность нанесения прозрачной полосы для просмотра уровня жидкости, т.к. подавляющие большинство подобных канистр делаются их окрашенного, непрозрачного полимера
- Станции пост-охлаждения для небольшого увеличения производительности
Канистры индивидуального дизайна объёмом больше или меньше 4–5 литров встречаются гораздо реже, поэтому типовых решений для них мы не озвучиваем, но уточним, что 10-литровые канистры очень часто можно разместить на номинально пятилитровых машинах. Здесь же отметим, что производство канистр (бутылок) без ручек объёмом 1 литр, часто сопровождающее производство канистр 4–5 литров, всегда лучше выносить на отдельную машину или машины.
2. Промышленные канистры широкого назначения
Товары промышленного свойства, где упаковка для покупателя не является сколько-нибудь весомым аргументом при выборе (например, специализированная химия не для личного применения) или потребительские товары с невысокой добавленной стоимостью (например, строительные смеси или автохимия нижнего и среднего ценового сегмента) упаковываются в стандартизированные канистры, которые не отличаются дизайнерскими изысками.
Производство канистр индивидуального дизайна обычно плотно привязано к потребителю канистр, а часто вообще находится на одной территории с линией розлива. При этом существует огромное множество компаний химической отрасли, нуждающихся в полимерной таре для своей продукции, но не имеющих достаточных объёмов, чтобы окупить экструзионно-выдувное оборудование для её производства.
Существует и небольшое количество компаний, которые одновременно являются потребителями и продавцами канистр (их минимум).
Все выше перечисленные категории компаний не производят канистры сами, а обращаются к специализированным производителям выдувной упаковки. Естественно, что для удовлетворения потребностей максимального количества потенциальных покупателей производители упаковки вынуждены максимально стандартизировать и упрощать форму выпускаемых ёмкостей.
Как следствие, промышленные канистры ориентированы не на подчёркивание дифференцирующих свойств товара или эмоционального наполнения брэнда, а на снижение издержек производства этих канистр. Они обладают отточенной с точки зрения экономии веса конструкцией и (если говорить о российском рынке) изготавливаются в большинстве своём из отечественного сырья, которое имеет худшие показатели стабильности от мешка к мешку, но зато стоит дешевле импортного на 5–15% в зависимости от текущей конъюктуры рынка.
Промышленные канистры можно разделить на две основные категории и одну дополнительную.
2.1 Канистры с внешней ручкой (нештабелируемые) – «Классика»
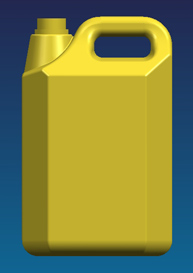
Канистры классической формы с обычным (наиболее очевидным) расположением ручки сверху и простым прямоугольным дизайном лучше позволяют наиболее оптимально распределить полимерную массу. 5-литровая канистра, приемлемая по прочности, может весить всего 170–180 гр. (до 150 гр. с системами профилирования рукава SFDR / PWDS), против 200–220 гр. (до 180 гр. с системами профилирования рукава SFDR / PWDS) для евроканистры такого же объёма (о евроканистрах речь пойдёт ниже).
Сегодня наиболее ходовой типоразмер канистр этого вида — 5 литров. Рекомендации по оборудованию для дизайнерских канистр 4–5 литров, высказанные выше, актуальны и для промышленной канистры такого же объёма за исключением того, что благодаря более низкому весу и более равномерному распределению массы цикл выдува меньше (он может быть в диапазоне 15–20 секунд), поэтому при той же гнёздности производительность будет на 20–40% больше чем указано в таблице).
Промышленные канистры объёмом 10 литров, которые не так популярны и в основном выпускаются в евродизайне, в большинстве случаев можно производить на тех же машинах при той же гнёздности, что и канистры 5 литров, но с увеличенными диаметрами шнеков экструдеров. Производительность при выдуве канистр 10 литров будет приблизительно на 20% ниже, чем производительность по 5-литровым канистрам при той же гнёздности.
Канистры с внешней ручкой объёмом больше, чем 10 литров производятся очень мало, а по канистрам объёмом меньше 4–5 литров, как сказано выше, сложно вывести какие-то типовые решения.
Наблюдая нынешние тенденции можно заключить, что канистры общего назначения объёмом 5–10 литров и выше всё больше выпускаются в дизайне с утопленной ручкой (об этом ниже). Однако, канистры с внешней ручкой по-прежнему производят и будут производить, т.к. они обеспечивают меньший вес, а значит меньшую стоимость канистры, а также более удобны для конечного пользователя (т.е. для обычного человека), чем канистры с утопленной ручкой. Удобство канистры для человеческого использования делает её привлекательной с маркетинговой точки зрения.
2.2 Канистры с утопленной ручкой (штабелируемые) – «Евро»
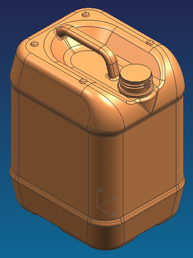
Логистика и всё больше правит экономическим миром. Стандартизированные штабелируемые канистры с утопленной ручкой — это часть концепции идеальной логистики. Такие канистры по своим внешним размерам идеально, используя всю площадь, устанавливаются на европоддоны (канистры этой конструкции также называют просто евроканистрами), а возможность установки прямо друг на друга без дополнительных прокладок и обрешётки позволяет обеспечить максимальную загрузку любого транспорта.
В штабелируемых канистрах ручка утоплена в «тело» канистры — она располагается в специальном углублении, сохраняя канистру «кубообразной». В верхней части канистры оформляются специальные фиксирующие штыри, а в дне — соответствующие пазы. Таким образом, когда канистра ставится на другую такую же канистру, штыри входят в пазы и обеспечивают устойчивость. Ручка при этом находится как бы внутри нижней канистры и не касается верхней. Стенки штабелируемых евроканистр должны быть достаточно массивными, чтобы выдерживать вес, установленный на них сверху (а это обычно несколько ярусов).
При производстве канистр с утопленной ручкой раскрытие прессформ должно происходить одновременно в двух направлениях — традиционным горизонтальным движением и дополнительным вертикальным движением. Вертикальное движение является необходимым для горизонтального раскрытия т.к. в противном случае прессформа «упрётся» в стенки канистры, расположенные вокруг утопленной в них ручки. Для этого прессформа должна состоять не из двух полуформ, а из четырёх элементов, а машины должны иметь дополнительные гидравлические приводы для активации цилиндров выдвигающих эти дополнительные элементы формы вертикально. Таким образом, к набору опций необходимых и рекомендуемых для производства обычных канистр (см. выше) добавляется:
- Контур управления гидравлическими (или пневматическими) цилиндрами прессформы для вертикального раскрытия.
- Канистра при горизонтальном раскрытии прессформы будет немного сползать вниз с выдувного дорна, следуя контурам стенок, поэтому выдувной дорн должен иметь дополнительный контур управления, чтобы также сдвинуться вниз (если дорн останется на месте, то канистра или упадёт с него или деформируется).
- Дополнительное устройство на верхних обрубочных масках для вырубки облоя из под ручки, находящейся в нише и не на линии действия прямой верхней обрубки.
- Узел смыкания должен быть достаточно большим, чтобы вместить не только основное тело прессформы, но и дополнительные цилиндры по бокам (или снизу), а также пространство для вертикальной раздвижки прессформы.
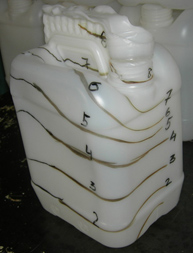
Главная технологическая особенность евроканистр — неоптимальное распределение массы. Канистры выдуваются из ровной трубчатой заготовки (рукава), которая в верхней части (район горловины, ручки, плечей) при смыкании вытягивается и складывается гармошкой для формирования утопленной зоны. Регулировка толщины стенки рукава (паризон-контроль) в этой зоне позволяет сконцентрировать достаточную толщину, чтобы при вытягивании рукава стенки в районе плеч канистры оставались прочными, однако, одновременно в зоне под горловиной и в зоне с противоположной стороны скапливается излишнее количество материала (своего рода «курдюк»), который там совершенно не нужен (он увеличивает и вес и время охлаждения). Лучше всего эту особенность иллюстрирует фотография справа.
Чёрные метки при нанесении на рукав в процессе его выхода из головки были горизонтальными полосами.
Учитывая эту специфику, в эффективном производстве евроканистр важнейшими элементами успеха являются оптимальный дизайн канистры, оптимальное сечение рукава и оптимальный профиль распределения массы.
Единственный способ убрать «курдюк» под горловиной — это система PWDS (и её аналоги), т.е. система радиального профилирования (овализации) рукава на лету в нужный момент цикла выхода рукава. PWDS — это горизонтальная ось регулирования профиля рукава, в то время как паризон-контроль — вертикальная. Вместе эти две опции позволяют, насколько это возможно, добиться оптимального распределения массы, что обеспечивает и минимальный вес и максимальную прочность.
2.2.1 Евроканистры 5–10 литров
Типовые решения для производства евроканистр 5 и 10 литров также весьма похожи на таблицу, представленную ранее. Цикл выдува евроканистр 5–10 л крутится вокруг 25 секунд, но сильно зависит не только от качества охлаждения прессформы, но и от степени регулирования профиля рукава. Так, если мы за счёт PWDS (или аналога) убираем «курдюк» под горловиной, то требуемое время охлаждения снижается значительно, ведь это утолщение приводит к наклону горловины вперёд в результате усадочных процессов, а чтобы его минимизировать приходится охлаждать канистру дольше. Нет «курдюка» — нет необходимости долго выдерживать канистру в прессформе.
Также время цикла зависит от количества и степени систем пост-охлаждения после выхода изделия из прессформы. Например, для евроканистры 10 л весом около 350 г цикл может доходить до всего 15 секунд, но после выдува канистра должна пройти ещё 5 станций пост-охлаждения (при этом сама канистра должна быть идеально отрегулирована по распределению массы). Это технически сложная и совсем не эргономичная система, где перенастройка на другие изделия (или иные изменения) на практике исключена. Всегда стоит рассмотреть возможность вместо экстремального сокращения времени цикла просто добавить ещё одно гнездо. Впрочем, производственные и коммерческие задачи у различных компаний отличаются, поэтому решения принимаются индивидуально.
2.2.2 Евроканистры 20–30 литров
Типоразмеры современных экструзионно-выдувных машин построены таким образом, что для выдува евроканистр 20–30 л на одном ручье подходит одна и та же модель и довольно часто эта же модель станка может производить канистры 10 л на двух ручьях. В связи с этим, оптимальным является разнести производство евроканистр 5–10 л и 20–30 л на разные машины в разной конфигурации.
Для евроканистр 20 и 30 л необходимость оптимизации не только вертикального, но и горизонтального регулирования толщины рукава только возрастает по сравнению с более мелкими канистрами; влияние на вес канистры и на время цикла этих систем становится ещё больше. Равно как и эффект от пост-охлаждения. На примере евроканистр 20 л при весе около 780-800 г цикл одной станции с двумя позициями пост-охлаждения может составить около 30 секунд. Цикл очень сильно зависит от допустимой степени утяжин на поверхности канистры и допустимой степени отклонения горловины от вертикальной оси (вспоминаем эффект от PWDS). В отсутствие PWDS и пост-охлаждения с водяным контуром время цикла может возрастать и до 40 секунд. А при использовании прессформ с неэффективными водяными каналами время цикла может превышать минуту.
Конфигурация машины под евроканистры 20–30 л это (почти) всегда 1 ручей и либо одна либо две станции, т.е. в итоге два основных варианта. При времени цикла 30 с (на 20 л) получается мощность производства либо до 80 тыс. канистр в месяц (100–120 шт/ч), либо до 160 тыс (200–240 шт/ч). Конечно, производительность может быть меньше в зависимости от факторов, описанных выше. Цикл на евроканистру 30 л при прочих равных на 5–10 с медленнее чем на 20 л, но потребление 30-литровых канистр на рынке всегда гораздо меньше.
Есть способ производства евроканистр 20–30 л на экструзионно-выдувных машинах с головками аккумуляторного (накопительного) типа с нижним расположением выдувного дорна, но такой принцип имеет явные недостатки:
- Невозможность нанесения прозрачной полосы уровня
- Большое количество облоя с донной стороны канистры (следствие большого расстояния от кромки прессформы до места обрезания рукава)
- Длинное время цикла из-за ожидания выдавливания порции рукава головкой началом смыкания прессформы
2.3 Штабелируемые канистры с внешней ручкой
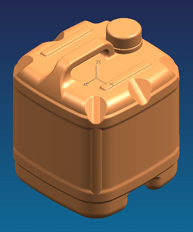
Редкий вид канистр по конструкции между евроканистрами и классическими канистрами с верхней ручкой. Суть штабелируемых канистр с внешней ручкой в том, что в дне делается углубление достаточное для помещения туда ручки, но углубление делается перпендикулярно ей, что позволяет раскрывать прессформу без вертикального движения. В результате канистры легко и чётко устанавливаются друг на друга после поворота на 90 градусов.
У таких канистр есть один существенный недостаток: они ограничены по дизайну и могут быть только квадратного сечения, что усложняет оптимальное паллетирование на поддонах.
Тем не менее, для некоторых специальных задач подобные канистры могут быть использованы. По весу и сложности оборудования они наиболее близки к обычным нештабелируемым канистрам, что делает их производство более доступным по сравнению с евроканистрами.
А как же канистры со стрип полосой?
Нанесение прозрачной полосы уровня — это просто опция экструзионной головки. Она не создаёт дополнительную категорию канистр, а может быть применена к любому из перечисленных (или не перечисленных) типов канистр.