Статья впервые опубликована в сети 02 декабря 2015 года, а также в №8, 2015 журнала «Пластикс» / Обновлена 18 сентября 2023 года
Как и во многих других методах переработки пластмасс, в экструзионно-выдувном формовании присутствует процесс смыкания. Здесь две полуформы прессформы сжимают заготовку (расплавленный экструзионный рукав), давая старт процессу дальнейшего формования готового изделия. В отличие, например, от литья под давлением процесс смыкания прессформы в экструзионно-выдувном формовании в гораздо меньшей степени пригоден для теоретических обсчётов «на берегу», менее предсказуем и, главное, менее изучен. Вместе с тем, смыкание прессформы в экструзионно-выдувном формовании имеет огромное влияние на весь технологический процесс, большее, чем кажется многим, поэтому понимать и правильно управлять им совершенно необходимо для организации эффективного производства.
Прежде всего, следует разобраться с базовыми вещами и некоторой терминологией. Смыкание в ЭВ-формовании решает две задачи. Первая задача состоит в том, чтобы пережать кромку, разделяющую заготовку (фрагмент рукава) на часть, идущую на формование изделия, и на часть, остающуюся на облой. Вторая задача — противодействовать открытию прессформы вследствие давления сжатого воздуха, подаваемого внутрь заготовки для её формования.
Линия пережатия
Ключевое понятие при изучении смыкания прессформы — линия пережатия. Линией пережатия (в англоязычной терминологии — pinch line) считается вся длина вышеупомянутой кромки, пережимаемая прессформой для отделения полезной части заготовки от облоя. Область прессформы, ответственная за это действие, называется обрезной кромкой (cutting edge).
Длина линии пережатия в первую очередь зависит от дизайна изделия, и здесь их все можно классифицировать на четыре основные группы:
А) Ёмкости без плечевого облоя
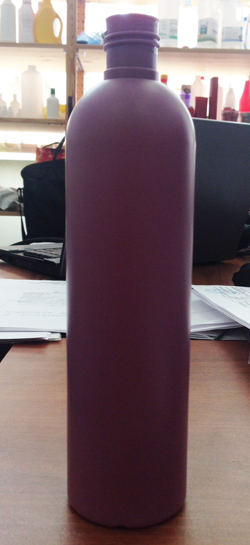
Это, как правило, самые простые флаконы, бутылки и банки, где разница в диаметре горловины и основного тела изделия не столь велика, и, таким образом, рукав по своей ширине не заходит за пределы горловины. При выдуве таких изделий линия пережатия возникает только по дну флакона и очень часто даже не во всю его ширину.
Б) Ёмкости с плечевым облоем
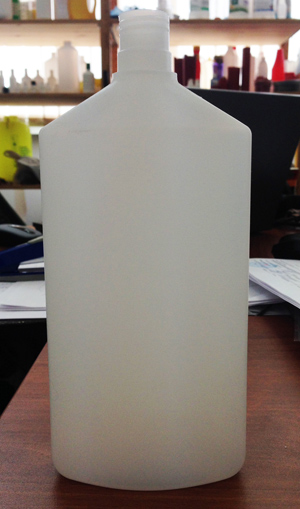
Сюда можно отнести широкие, овальные, плоские флаконы или круглые бутылки, где разница в диаметре горловины и ширины тела довольно большая (более 3-4 раз). Раздуть подобные изделия из узкого рукава не получается из-за плохого распределения материала на наиболее удалённые фрагменты и углы флакона, поэтому рукав делают широким, и при смыкании прессформы линия пережатия появляется не только по дну, но и слева, и справа от горловины на т.н. плечах флакона.
В) Ёмкости с ручкой
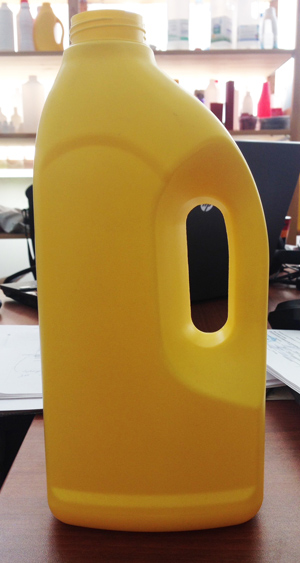
Бутылки и флаконы с ручкой, канистры можно отнести к своей отдельной категории. При производстве этих изделий рукав в любом случае должен быть достаточно широким, чтобы полностью охватить ручку (в противном случае ручка просто не будет раздута). Это, во-первых, означает, что, скорее всего, рукав по ширине будет практически совпадать с общей шириной изделия, а значит линия пережатия будет идти и по всему дну и по всем плечам (или по большей их части). Во-вторых, линия пережатия пройдёт также по всему внутреннему контуру ручки, ведь фрагмент рукава, оказавшийся внутри неё, относится к облою и требует пережатия. Если у изделия две ручки, то его линия пережатия будет ещё больше.
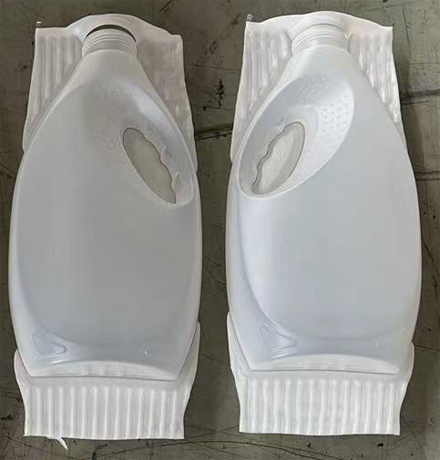
Г) Технические изделия
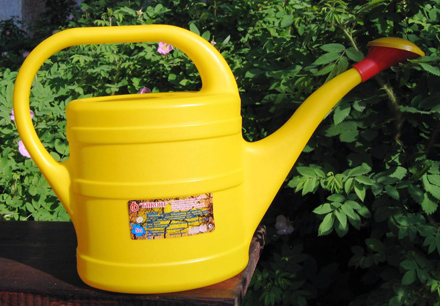
К этой группе для простоты обобщения мы относим все сложные по геометрической форме изделия неупаковочного применения. Самые яркие примеры: садовые лейки или автомобильные воздуховоды. У таких изделий зачастую длина линии пережатия равняется длине всего контура конечной детали, или же составляет 60–90% длины этого контура.
Далее возникает вопрос как трансформировать полученное значение длины линии пережатия в требование по усилию смыкания. На этот предмет в иностранной литературе можно встретить целый ряд рассуждений и расчётов, но по результатам реальной работы наиболее точной и простой для понимания показала себя следующая формула:
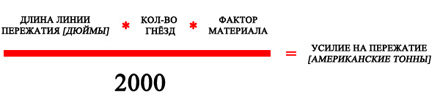
Фактор материала введён поскольку в ЭВ-формовании используется не только полиэтилен низкого давления, но и другие материалы, такие как ПЭВД, ПП, ПК или сополиэфиры ПЭТ, и требуемое усилие пережатия для данных материалов различается довольно сильно. Для указанной формулы фактор материала выведен следующим образом:
- ПЭНД – 550
- ПЭВД – 450
- ПП – 950
- ПК / Сополиэфиры – 1100-1200
Формула неслучайно приведена в «американских» единицах измерения, ведь именно в США экструзионно-выдувное формование получило наиболее широкое и массовое применение, и наибольшее количество специалистов-практиков по выдуву работает именно в этой стране.
Если упростить формулу и перевести её в более привычную нам метрическую систему измерений, то получим, что для пережатия 1 см ПЭНД требуется приблизительно 1 кН усилия (для ПЭВД соответственно 0,8 кН, для ПП — 1,65 кН, а для ПК и Сополиэфиров около 2–2,2 кН). Очень важно уяснить и всегда помнить, что длина линия пережатия изделия прямо пропорционально влияет на требуемое усилие, а также то, что длину линии пережатия изделия всегда необходимо умножать на количество гнёзд в прессформе.
Сжатый воздух
Вы могли обратить внимание, что в вышеприведённой формуле результирующее значение называется усилием пережатия (а не усилием смыкания). Чтобы рассчитать общее усилие смыкания, необходимо также учесть влияние сжатого воздуха.
Усилие, требуемое для запирания прессформы против сжатого воздуха, считается классическим методом: умножением площади проекции изделия на давление воздуха. Например, если у нас прямоугольный плоский флакон с шириной 6 см и длиной 12 см, и если мы выдуваем его давлением воздуха в 7 бар, то для противодействия воздуху необходимо примерно 5 кН усилия на каждое гнездо такого флакона. Площадь проекции горловины в расчёте не участвует, поскольку выдувной дорн её полностью закрывает. Для более геометрически сложных форм площадь проекции считается с большей скрупулёзностью, но в целом вполне допустим и её приблизительный расчёт с некоторым запасом в большую сторону.
Основной спорный момент заключается в том, как сопоставлять полученное требование по усилию пережатия и требование по усилию запирания против сжатого воздуха. Некоторые англоязычные источники утверждают, что следует опираться на большее из полученных значений, поскольку сначала происходит пережатие облоя, а лишь затем после полного смыкания прессформы подаётся воздух, и, таким образом, это якобы последовательные никак не пересекающиеся процессы. Теоретически это утверждение кажется верным, но реальный практический опыт автора показал, что процессы пережатия кромки и противодействия сжатому воздуху всё-таки связаны.
Та грань, где заканчивается пережатие и начинается давление выдува, на самом деле размыта и зависит от множества параметров технологического процесса, таких как скорость и динамика смыкания прессформы, настройки стадий выдува, дизайна самого изделия, конструкции пресс-канта и др. Мы настоятельно рекомендуем для гарантированного исключения ошибок при подборе общего усилия смыкания для проекта суммировать рассчитанное усилие для пережатия кромки с усилием противодействия сжатому воздуху — очень велика вероятность, что в какой-то, пусть и небольшой, промежуток эти два усилия будут действовать одновременно, и этого будет достаточно для возникновения негативных эффектов (о них в конце статьи).
Так автор работал, в частности, с проектом, где уменьшение давления воздуха с 8 до 4 бар снижало усилие по расчётам на 20 кН — с 160 кН до 140 кН (оба значения с учётом всех гнёзд и суммы усилия пережатия и усилия противодействия воздуху). При этом усилие смыкания, создаваемое машиной, составляло 150 кН, и его хватало для работы при давлении воздуха 4 бара, но уже не хватало для работы с давлением 8 бар, т.е. в данном случае совершенно точно общее требуемое усилие составляло полную сумму двух обсуждаемых типов усилий, несмотря на теоретические выкладки о последовательности процессов.
В машинах с электрическим приводом смыкания, реализованным посредством кривошипного механизма (а так сделано большинство электрических экструзионно-выдувных машин), усилие пережатия можно считать изолированным от усилия запирания против сжатого воздуха в том случае, когда кривошипный механизм встаёт полностью «в распор». При подобном положении рычагов чисто механически сжатый воздух не может оказать никакого существенного влияние на скрепляемость полуформ, поэтому усилие пережатия остаётся единственным параметром для расчёта.
Реализация усилия смыкания
Создаваемое станком усилие смыкания для гидравлических выдувных машин определяется двумя равнозначными факторами: типоразмером гидроцилиндра смыкания и давлением масла, подаваемым в цилиндр в момент запирания. Поскольку в экструзионно-выдувных машинах механизм узла смыкания, как правило, имеет довольно простую кинематику, то принято считать, что обеспечиваемое усилие смыкания приравнивается к номинальному толкающему усилию гидроцилиндра. Толкающее усилие, в свою очередь, высчитывается стандартным способом, принятым в гидравлической науке, а именно умножением давления масла на площадь гильзы (bore в англоязычной терминологии) цилиндра. Так гидравлический цилиндр с гильзой диаметром 125 мм при давлении масла 100 бар обеспечивает усилие в 122 кН.
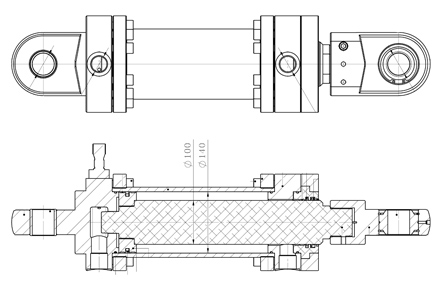
Если диаметр гильзы цилиндра фиксирован и известен заранее, то давление масла является переменной величиной. При работе машины давление гидравлического масла, во-первых, изменяется динамически по мере его расхода на обеспечение движений различных цилиндров, во-вторых, регулируется с помощью предохранительного клапана. В результате, чтобы понять какое конкретно усилие обеспечивается гидроцилиндром, необходимо отследить под каким давлением масло подаётся в него именно в момент смыкания. Зачастую в момент смыкания система не может обеспечить такое же давление масла, как во время других фаз работы машины (например, 80–90 бар в момент смыкания при 110–120 барах в другие моменты), поэтому, изучая «каталожные» значения параметров усилия смыкания, при выборе конфигурации машины важно точно выяснить при каком давлении масла обеспечивается заявленное усилие, и обеспечит ли вообще гидросистема такое давление при реальной работе.
По обеспечиваемому давлению гидравлические системы экструзионно-выдувных машин можно разделить на три условные категории: системы с рабочим давлением 80–120 бар, с рабочим давлением 140–160 бар и с рабочим давлением 180–220 бар. Конечно, это не жёсткие нормативы, и существуют промежуточные системы, а также системы, работающие с более широким диапазоном (например, от 120 до 220 бар). Существуют также комбинированные системы, где на смыкание прессформы отведён отдельный гидравлический контур со своим насосом и со своим рабочим давлением, в то время как остальные движения обслуживает контур с более низким давлением.
Гидросистемы с давлением 80–120 бар обычно способны обеспечить усилие смыкания не более 100–150 кН — чтобы «выжать» из них больше, цилиндр смыкания должен быть несоразмерно большим, что влечёт и механический дисбаланс, и чрезмерное время на заполнение маслом такого цилиндра. Для средне- и крупнотоннажных машин (150–300 кН) наиболее рациональными выглядят системы с раздельным контуром на смыкание и на остальные движения. Это позволяет использовать высокое давление только там где это действительно нужно (на смыкание), а для менее ответственных, с точки зрения усилия движений (каретка, выдувной дорн, кивок, обрубки), использовать небольшое давление (например, 80–90 бар), что обеспечивает лучшие условия эксплуатации и долговечность гидравлических комплектующих.
Разновидности узлов смыкания экструзионно-выдувных машин
Более или менее все варианты исполнения узлов смыкания экструзионно-выдувной машины можно разбить на следующие категории.
Узел смыкания с двумя направляющими колоннами по противоположным углам плиты
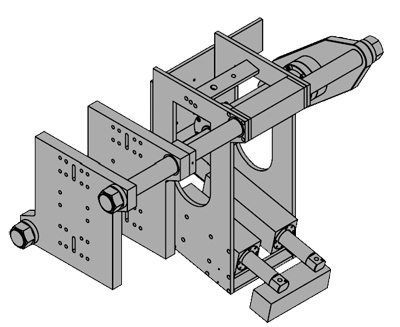
Цилиндр смыкания расположен сзади по центру плиты. Раскрываясь, цилиндр давит на центр задней плиты и синхронным усилием другим концом притягивает переднюю плиту по двум направляющим колоннам, расположенным в правом нижнем углу и в левом верхнем.
Это первый узел смыкания, с которого вообще начались в 1960-х годах экструзионно-выдувные машины с верхним выдувом и кареткой, перемещающейся из позиции «под головкой» в позицию «под выдувным дорном». Данная концепция обеспечивает очень хорошее распределение усилия по поверхности плиты, и её единственный минус — невозможность передачи изделия на позицию автоматического удаления облоя (мешает правая верхняя колонна).
Узел смыкания с нижним расположением направляющих колонн
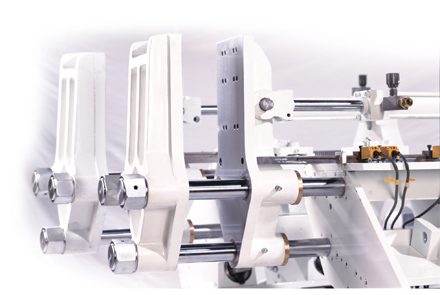
Для возможности передачи изделий в сторону в позицию для удаления облоя был разработан узел смыкания с нижним расположением направляющих колонн. Принцип синхронного давления на центр задней плиты с одновременным притягиванием передней сохранился, но колонны расположены не по углам, а снизу.
Вариация с нижним расположением колонн с системой вертикальной балансировки
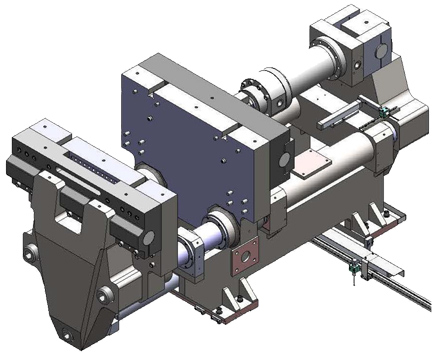
Проблема с нижними направляющими в том, что передняя плита тянется колоннами за нижнюю часть, создавая дисбаланс в распределении усилия смыкания по вертикальной оси. Чтобы исправить этот недостаток разработан более совершенный узел, где нижние направляющие тянут не саму плиту смыкания, а дополнительную скобу, которая в свою очередь тащит вместе с собой и переднюю плиту. Точкой контакта между скобой и передней плитой является палец-шарнир, расположенный приблизительно посередине передней плиты смыкания. При возникновении сопротивления в виде требующей перерезания кромки шарнирная система позволяет равномерно распределить усилие смыкания по всей поверхности плиты.
Рычажный узел смыкания
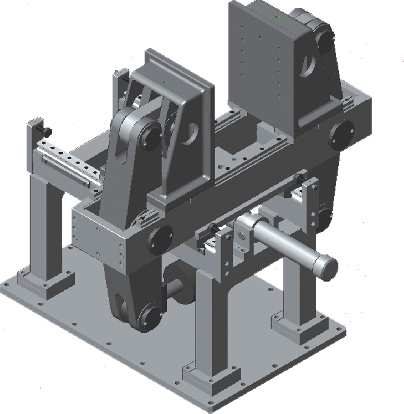
Усилие смыкания создаётся гидроцилиндром, расположенным снизу под плитами. Цилиндр по принципу ножниц раскрывает в нижней части рычаги узла смыкания, которые, в свою очередь, запираются в верхней части, создавая равномерное и одинаковое усилие смыкания на плиты.
Рычажный узел смыкания вообще не имеет направляющих колонн (плиты перемещаются по полозьям).
Рычажный узел смыкания (горизонтальный)
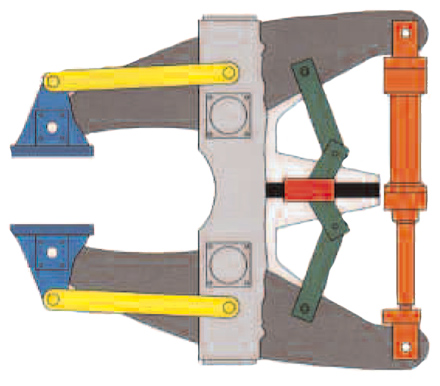
Более старый вариант рычажного узла смыкания многие десятилетия использовался известным немецким производителем экструзионно-выдувных машин и одним менее известным итальянским (в отличие от описанной выше версии рычаги располагаются параллельно полу, а не перпендикулярно). На схеме представлен вид сверху. В таком варианте баланс распределения усилий достигается за счёт физически громоздких и, как следствие, механически мощных элементов системы: рычагов, рамы, пальцев и т.п. Это же и стало причиной постепенного отказа от подобных узлов — чрезмерные габариты и страдающая эргономика экструзионно-выдувной машины.
Крупногабаритный узел смыкания с двумя гидроцилиндрами
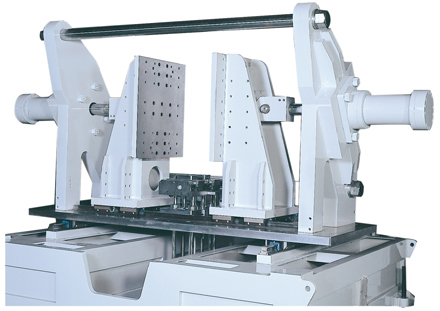
На крупнотоннажных машинах с головками аккумуляторного типа обычно не используются различного рода рычажные или притягивающие механизмы. В подобных машинах на каждую из двух плит просто ставится отдельный гидроцилиндр, который толкает свою плиту одновременно с противоположным цилиндром, который толкает свою. Плиты могут перемещаться как по полозьям, так и по направляющим колоннам, в зависимости от конфигурации конкретного станка.
У машин данного типа итоговое создаваемое усилие смыкания является суммой усилий сразу двух цилиндров, поэтому даже при умеренном типоразмере гидроцилиндров оно может составлять 400–600 кН.
Узел смыкания с гидрозамками
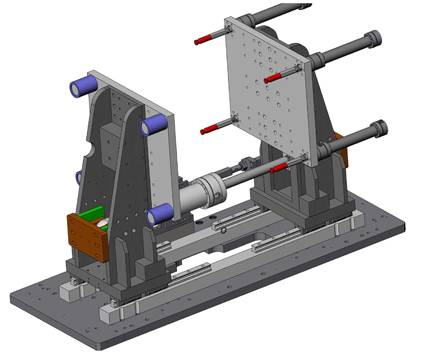
Этот специализированный тип узла смыкания не столь распространён, однако благодаря своей уникальности обязан быть упомянут в обзоре.
Последовательность работы узла смыкания с гидрозамками выглядит следующим образом:
- Нижний гидроцилиндр смыкает прессформу.
- Четыре цилиндра по углам плиты заводят штоки в специальные механические гидрозамки.
- Замки автоматически закрываются и зажимают штоки.
- Затем все четыре цилиндра переключаются на тянущее усилие.
- Поскольку замки держат штоки, тянущее усилие четырьмя цилиндрами ещё больше прижимает плиты и, самое главное, обеспечивает распределение усилия по всей поверхности плиты гораздо лучше, чем когда один цилиндр давит более или менее на центр.
Узел смыкания с гидрозамками применяется, например, в машинах для производства сверхкрупных изделий, таких как 200-литровые бочки (в последнем случае это обычно комбинация узла с замками и крупногабаритного узла с двумя цилиндрами).
Распределение усилия смыкания по поверхности
Описанный последним тип узла смыкания с замками плавно выводит нас к важнейшей теме о распределении создаваемого гидроцилиндрами усилия смыкания по поверхности плит и прессформы. Распределение имеет не менее принципиальное значение, чем длина линии пережатия, давление воздуха или генерируемое цилиндром усилие, однако, к сожалению, не поддаётся точному расчёту.
Основы правильного распределения усилия смыкания сводятся к отсутствию чрезмерных перекосов между точкой приложения давления и областью его применения. Причём особое значение имеет именно вертикальная ось, т.к. по горизонтали балансировка достигается проще и в основном не является трудностью. Яркий пример перекоса приведён на схеме:
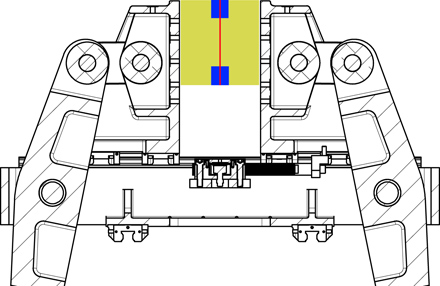
Узел смыкания с двумя направляющими колоннами по противоположным углам очень хорошо распределяет усилие по поверхности плиты за счёт широкого «обхвата» плит в комбинации с простотой механизма прямого действия. Ещё эффективнее работает узел смыкания с гидрозамками: благодаря одновременному давлению и на центр, и, главное, на все четыре угла плиты, достигается практически идеальное распределение усилия смыкания. Особенно если размер прессформы приближен к размеру самой плиты, и области линии пережатия более или менее равномерно распределены по периметру изделия.
Пример из практики автора: настраивая узел смыкания экструзионно-выдувной машины с гидрозамками, мы могли воочию убедиться, насколько большой эффект имеет баланс распределения усилия смыкания по поверхности плиты, нежели просто большое усилие, применённое не на ту точку.
Нижний цилиндр смыкания обеспечивал толкающее усилие до 200 кН, при этом для производимых на данном станке канистр объёмом 20 и 30 литров должно было хватать по расчётам 160 и 175 кН соответственно. Однако при работе лишь одного этого цилиндра, несмотря на его номинальную достаточность для данной задачи, качество пережатия облоя было нечётким и нестабильным.
Если приглядеться к тому, как данный цилиндр механически прикреплён к плитам, то становится очевидным некоторый перекос: цилиндр больше стягивает плиты в нижней части. Но как только были активированы четыре дополнительных гидроцилиндра по углам плит, то баланс был достигнут незамедлительно — пережатие стало не просто лучше, оно стало идеальным, даже не взирая на не самое высокое качество той прессформы. Причём четыре угловых цилиндра работали на тянущем усилии и обеспечивали всего по 15 кН каждый, тем не менее эффект от их давления был не столько в цифрах, сколько в «натуральном выражении»: облой отваливался ещё до поступления в узел обрубки.
Как мы выяснили, узлы смыкания с двумя противоположно расположенными колоннами и узлы с гидрозамками имеют наилучшее распределение давления, но на практике в подавляющем большинстве экструзионно-выдувных проектов они не применяются из-за других своих ограничений. Выбор преимущественно происходит между рычажным узлом смыкания и узлами с нижним расположением колонн.
Вертикальный дисбаланс применения усилия смыкания на рычажном узле, меняющийся в зависимости от длины прессформы и дизайна изделия, обсудили чуть выше. Что касается узлов с нижним расположением колонн, то в выигрыше всегда будут версии с балансировочным шарниром (при условии правильной механической конструкции узла в целом).
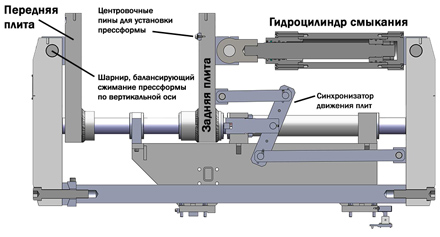
В узле, представленном на схеме выше, передняя и задняя плиты смыкания жёстко закреплены в мощных направляющих колоннах и «не гуляют», но, вместе с тем, усилие смыкания применяется на переднюю плиту не притягиванием за эти же колонны, а через шарнирный палец, соединяющий скобу и переднюю плиту. Зона пережатия облоя всегда распределена неравномерно в вертикальной оси, и шарнир при полном смыкании прессформы естественным образом находит не продавленные области и дожимает их. Не за счёт механического перекоса (крена) плиты, а за счёт перераспределения усилия.
В этом недостаток даже очень хороших узлов с нижним расположением колонн, но без шарнира. Они могут обеспечивать очень хорошее распределение усилия по всей поверхности плиты благодаря грамотно рассчитанной механике и качеству исполнения. Эти машины будут иметь впечатляюще равные показатели с тестовых тензодатчиков (измерители усилия), которые поставят по четырём углам плиты. Но в реальном экструзионно-выдувном формовании усилие требуется на каждой прессформе в разных точках плиты, и в этой связи некоторая степень свободы перераспределения усилия за счёт шарнирной конструкции улучшает процесс.
Примечание: Как отличается распределение усилия смыкания по поверхности плиты, если мы имеем электрический привод на этот контур, а не гидравлический? Никак. В электрической экструзионно-выдувной машине место гидроцилиндра смыкания занимает кривошипный механизм, поворачиваемый сервомотором, но кинематика узла смыкания не меняется.
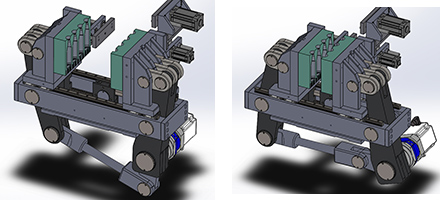
Качество распределения усилия сжатия по прессформе столь же важно как и значение силы, номинально создаваемой актуатором. Оптимизация распределения этой силы нередко может позволить снизить количество кН, требуемое для хорошего перерезания кромки, на 10-20-30%.
Последствия недостаточного смыкания
Основная причина появления данной статьи как раз и состоит в необходимости выявления и обсуждения негативных последствий и эффектов, возникающих при недостатке смыкания (мы специально не употребляем термин «усилие смыкания», ведь, как мы выяснили выше, дело не только в усилии, но и в его распределении). Итак, попробуем систематизировать возникающие неприятности.
Первое и основное — это неуверенная обрубка облоя из-за плохого пережатия кромок. Плохим пережатием можно считать любую ситуацию, когда облой с изделия нельзя оторвать (или выбить) руками без специальных инструментов. Часто бывает так, что облой руками не отрывается, но машинные приводы вроде бы его всё-таки выбивают — такой режим работы должен настораживать, потому что обрубка в подобном режиме всегда будет нестабильной: при вас облой ещё отрубится, а в ночную смену будет оставаться на флаконе или застревать в подвижных частях машины. Если облой свободно отрывается рукой, то при обрубке машинными устройствами он должен не с напряжением тянуться, отделяясь от изделия, а без сопротивления и по хорошей траектории отлетать относительно одинаково каждый цикл или даже отваливаться от флакона после открытия прессформы ещё до попадания в позицию обрубки. Именно таким всегда будет режим работы при достаточном пережатии кромок.
Другая проблема — это качество следа на линии пережатия после отделения облоя. Бахрома, заусенцы и просто слишком выдающаяся остаточная полоса от облоя — всё это прямое следствие недостаточного смыкания. В большинстве случаев эти дефекты сопровождаются ещё и ранее обсуждённой плохой обрубкой. При подобных осложнениях все очень часто смотрят на качество и толщину обрезных кромок прессформы, но это неверный подход — прежде всего надо смотреть на усилие и распределение смыкания. Как показала практика, чтобы получить т.н. «нулевой» облой (след не более 0,2 мм по высоте от поверхности изделия), кромка вовсе не должна быть острой в прямом смысле этого слова. Кромки шириной 0,4–0,5 мм (а иногда и 1 мм) при должном смыкании вполне достаточно для максимально чистого отделения облоя. Пытаясь найти причину не в том месте, переработчики заостряют обрезную кромку до 0,2 мм и менее, что иногда даёт временное улучшение, но вскоре приводит к чрезмерному износу пресс-канта и ещё большему усугублению ситуации.
Безусловно, и фактор прессформы имеет немалое значение. Очевидно, что малейшее занижение или завышение формообразующих фрагментов или фрагментов пресс-канта относительно поверхности соприкосновения полуформ влечёт к возникновению перекосов. Точно также износ или механические повреждения самой обрезной кромки приведут к возникновению «недожатий» в этих критичных местах. Ещё один нюанс состоит в глубине полостей для размещения облоя (об этом мы писали в материале о производительности): при недостаточной глубине этих полостей чрезмерные сгустки облоя просто не позволят прессформе до конца сомкнуться, т.к. их некуда будет выдавливать.
Если вы испытываете трудности с обрубкой облоя и/или с качеством следов после его удаления, то первое, что следует сделать это убедиться в достаточности смыкания. Самый простой способ это проверить (если у вас многогнёздная прессформа) — механически заглушить один или несколько ручьёв. Также можно попробовать снизить давление выдувного воздуха. Если проблема уменьшилась или полностью ушла, значит вы нашли причину.
Конечно, существуют различные технологические ухищрения частично помогающие работать даже при недостатке смыкания, это, например, увеличение скорости закрытия (тогда плиты за счёт некоторой инерции могут чуть лучше пережать облой), или увеличение времени охлаждения (более остывший облой легче рубится). Но любые подобные решения лишь отчасти помогают, да и у них есть минусы (слишком быстрое смыкание может вести к неверному складыванию рукава и ослаблению сварного шва, а увеличение времени охлаждения снижает производительность), поэтому в конечном итоге для нормальной работы вам всё равно понадобится налаживать смыкание. Идеальное решение — заняться этим ещё на стадии подбора машины.
Спасибо! Отличное изложение и полезный материал
Благодарим за отзыв. Если есть предметные вопросы — обращайтесь.
Спасибо!!!
Очень полезный мануал. Спасибо!!!