Переход с выпуска одного на выпуск следующего по производственной программе изделия (что кратко можно назвать «сменой формата») на экструзионно-выдувной машине — это нечто большее, чем только замена прессформы. Во-первых, и на самой замене прессформы необходимо остановится подробнее, а, во-вторых, кроме прессформы надо заменять и перенастраивать ещё немало компонентов, что вкупе создаёт широкое пространство как для удлинения и усложнения всего процесса смены формата, так и возможности по его оптимизации.
1. Замена прессформы
1.1 Механизм
Каким техническим грузоподъёмным средством снять прессформы с обычного термопластавтомата лежит на поверхности — между колоннами узла смыкания есть открытое пространство, соответственно любое стабильное подъёмное устройство типа кран-балки может подцепить и просто вертикально поднять оснастку (и также опустить между колоннами подлежащую установке). В экструзионно-выдувной машине узел смыкания всегда находится или под головкой, или под выдувными дорнами, т.е. открытого вертикального доступа нет.
В совсем маленьких типоразмерах станков, где площадь прессформ укладывается в габариты около 200 х 200 мм, вопрос решается в прямом смысле руками, т.к. одну или обе полуформы может поднять человек и закрепить на плитах. Но это идеальный вариант. В большинстве эксплуатируемых экструзионно-выдувных машин габариты прессформ больше, и поднимать их руками становится невозможным, в т.ч. потому, что даже подняв, впихивать их потом боком в узел смыкания и, придерживая, закручивать категорически неудобно.
Здесь начинается «народное творчество» по подбору вариантов грузоподъёмной техники, где окончательный выбор будет зависеть от конструкции конкретной экструзионно-выдувной машины, имеющегося (или доступного к приобретению) парка грузоподъёмных средств и технической культуры предприятия, а также степени технического риска, допустимого на предприятии (последнее можно считать и частью технической культуры).
Среди неудачных (читай длинных и трудоёмких), но тем не менее используемых на заводах, процедур заноса прессформ можно выделить такие, как полное снятие выдувной калибровочной станции, либо экструзионной головки, и установка прессформы кран-балкой сверху в освободившееся пространство.
Среди рискованных (читай тоже неудачных) процедур можно назвать любые, связанные с применением погрузчика. Погрузчик, перемещающийся около высокотехнологичного оборудования — это всегда риск неосторожного движения, приводящего к повреждениям машины или оснастки и иногда довольно критичным.
Говоря о наиболее правильных и рекомендуемых способах заноса прессформы надо разделить их на два основных типа:
- Подвешивание прессформы
- Закатывание прессформы
Подвешивание прессформы предполагает, что она висит на крюке подъёмного устройства и заносится в узел смыкания сверху, или открытый узел смыкания перемещается в сторону висящей прессформы, и таким образом она оказывается между плит.
Классический вариант для такого способа — обычная кран-балка. Также это может быть козловой кран или краны, закреплённые непосредственно на раме станка: встречаются конструкции Г-образного крана на одном из передних углов рамы, либо «четырёхлапая» структура, прикреплённая к четырём углам рамы машины.
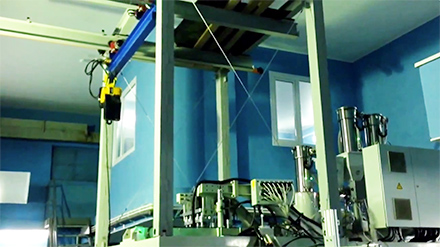
Из «подкатных» решений рабочими вариантами являются специальные мобильные краны-манипуляторы и штабелёры. Вес экструзионно-выдувных прессформ редко превышает 300–400 кг (например, прессформа на 5 л канистру на 2 гнезда из алюминия со стальными элементами весит около 350 кг), так что грузоподъёмность, требуемую от устройств, огромной не назовёшь.
Для удобного подвешивания и заноса прессформы от конструктива экструзионно-выдувной машины настоятельно рекомендуется иметь возможность отодвигания (в той или иной степени) калибровочной выдувной станции. При полном отодвигании (на расстояние одного хода каретки, например) прессформу можно просто опустить в узел смыкания сверху; при частичном — останется достаточно пространства для прокидывания строп крана, что легко позволяет подвесить прессформу во внутренней области машины и затем переместить «на неё» узел смыкания с тем, чтобы прессформа оказалась внутри.
|
Наилучшим образом подвешивание прессформы работает для узлов смыкания стягивающего типа с «висящими плитами» (подробнее о типах узлов смыкания экструзионно-выдувных машин рассказывается в другой нашей статье, здесь возвращаться к этому не будем). В таких станках прессформу перед началом подъёма можно удобно расположить на полу уже внутри защитных ограждений, и при подъёме стропам ничего не мешает. Также довольно легко использовать штабелёры (снизу в передней части станка для них нет препятствий).
В машинах с рычажными узлами смыкания прессформу положить внутри станка некуда, и в рабочую зону приходится их заносить уже подвешенными, поэтому из технических средств подходят только внутрицеховые мобильные краны, или надо полностью убирать калибровочную станцию (что не всегда можно сделать быстро и удобно).
В качестве решения по заносу прессформ в машины с рычажным узлом смыкания и/или для цехов с экстремально низкой высотой потолков существует способ с закатыванием прессформы сбоку (со стороны обрубки облоя). Для реализации такого метода используются тележки с небольшими рольгангами, которые по длине покрывают путь от свободной области сбоку от станка (где можно легко положить прессформу на тележку) до позиции каретки под выдувными дорнами.
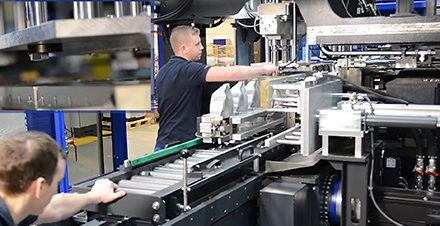
Подобные тележки разрабатываются индивидуально не только под конкретный тип экструзионно-выдувной машины, но и под конкретную модель и конкретную конфигурацию. Как правило, их и приобрести возможно только вместе с машиной у того же производителя/поставщика.
1.2 Крепление и центровка
В условной «обычной недорогой» экструзионно-выдувной машине для крепления прессформ вам будут предложены плоские плиты со сквозными отверстиями под болты. Резьба выполняется не в машинной плите, а в самой прессформе, поэтому болт просто прижимает её через плиту. И здесь кроется одна проблема: наружный диаметр резьбы болта всегда меньше диаметра отверстия в плите (остаётся небольшой зазор около 1 мм), следовательно, положение прессформы в горизонтальной и вертикальной осях после затяжки болтов не является одинаковым от установки к установке.
Это означает, что выдувной дорн попадёт не в одну и ту же точку горловой обрезной пластины прессформы (если сам выдувной дорн остался прежним в прежнем положении). Кроме того, при навешивании двух полуформ раздельно на каждую плиту — это создаст их несовпадение при смыкании. Возникает необходимость центровки.
Самый известный и понятный в механике способ центровки деталей относительно друг друга — это различные направляющие кольца, пазы, пины и т.п. (с соответствующими ответными частями). Казалось бы, очевидные вещи, но что-либо из этого есть далеко не во всех экструзионно-выдувных машинах, а только в тех, которые можно отнести к условной категории «нормальных» и выше.
Первичный и самый базовый способ для центровки прессформ заключается в наличии паза по центру монтажной плиты экструзионно-выдувной машины и ответной прямоугольной шпонки в прессформе. При попадании шпонки в паз прессформа окажется зафиксированной в горизонтальной оси.
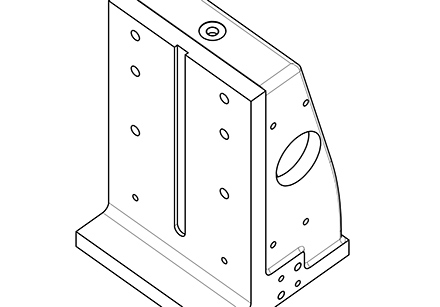
Вариацией такого исполнения является крестовой паз (к вертикальному добавляется горизонтальный) и соответствующая ответная шпонка в прессформе. При сочленении деталей прессформа примет фиксированное положение в обеих осях.
Однако, длинные пазы небольшой глубины не всегда обеспечивают удобную быструю стыковку деталей при неустойчивом положении навешиваемой прессформы (например, если она чуть болтается на крюке), и лучше работает пара круглых центрирующих пинов с большой фаской с соответствующими ответными отверстиями. За счёт круглой формы и конусной верхней части пины легко находят соответствующие отверстия, и прессформа быстро встаёт в правильном положении, далее лишь остаётся затянуть болты.
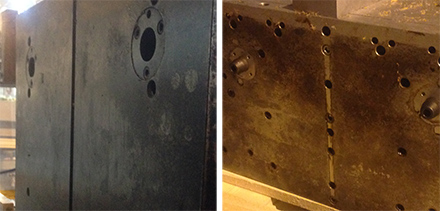
Существуют также варианты расположения пазов для центровки в виде квадратных выемок в верхней части плиты, а ответными частями в прессформе в этом случае являются цилиндры, наружный диаметр которых с маленьким допуском соответствует ширине выемки. В такой конструкции прессформу удобно опускать на плиту сверху — центровочные цилиндры легко попадут в соответствующие пазы-выемки, и прессформа при дальнейшем опускании автоматически «ляжет» в нужное положение как по горизонтали, так и по вертикали.
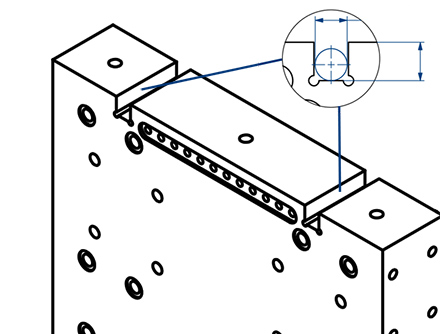
Если возвращаться к самому прикреплению прессформы к плитам, то ряд производителей (в основном немецких) предлагает вместо классических болтов использовать различные виды прижимов (активирующихся рычагами), или вариации крюков, с тем чтобы прессформу можно было легко «набросить» на них и затем прижать. В последнее время появились также эксперименты с использованием магнитных плит.
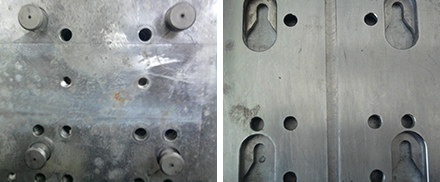
Эти вариации позволяют немного сократить по времени стадию прикрепления прессформы к плитам, но стоит помнить и о создании дополнительных усложнений конструктива машины и прессформы. В особенности важно последнее. Многим (если не большинству) переработчиков со временем приходится иметь дело с большим количеством разных прессформ, зачастую разных производителей или вообще предоставляемых заказчиком в аренду. Чем более нестандартным является способ крепежа прессформы к плитам, тем сложнее адаптировать между собой прессформы разного происхождения, и/или, например, при заказе новой оснастки обеспечить возможность её тестирования перед отгрузкой на аналогичном оборудовании. Учитывая это, старые добрые болты для крепежа остаются нормальным рабочим решением, тем более, что если удобно сделано всё остальное, сам процесс их закручивания происходит довольно быстро и не принципиально «затягивает» переналадку.
1.3 Подвод охлаждающей воды
Любой процесс смены прессформы начинается с отключения подвода охлаждающей воды, а заканчивается её подключением. С точки зрения времени/трудозатрат имеют значение следующие факторы:
- Кол-во шлангов (трубок)
- Тип подключения (штуцера)
- Путь (изгибы) шланга
- Пространство при подключении
Обсуждение первого фактора сводится исключительно к вопросу проектирования прессформы. В любой прессформе каналы для воды так или иначе разветвлены на отдельные контуры (как минимум разбиты по гнёздам), поэтому делить поток приходится всегда. Это можно сделать внутри прессформы или снаружи. Чем больше деление водяного потока вынесено за пределы прессформы тем, естественно, большее количество шлангов потребуется для подвода охлаждения. Если смотреть через призму монтажа и удобства эксплуатации, в идеальной прессформе все коллекторы для распределения воды уже будут предусмотрены внутри, а пользователю достаточно воткнуть одну пару вход/выход на полуформу.
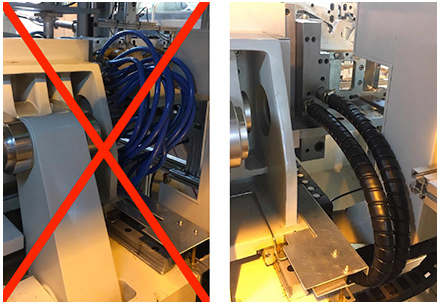
Исключением будут прессформы, где требуется индивидуальное температурное (или потоковое) регулирование на разные контуры (части изделия), но это разве что специальные применения типа выдува поликарбоната. Подавляющее большинство экструзионно-выдувных прессформ можно охлаждать водой одинаковой температуры и протока, поэтому мудрить с большим количеством шлангов нет смысла.
Тип штуцеров — вопрос исключительно слесарный и легко улучшаемый/ухудшаемый по месту. Для трубок в пределах 16 мм логично использование цанговых штуцеров, но стоит обращать внимание на их качество. Огромное количество доступных на рынке дешёвых штуцеров очень часто начинают быстро течь. Эти низкокачественные изделия, как правило, рассчитаны на работу только с воздухом (а не с водой) и с трудом переносят возникающие в экструзионно-выдувном оборудовании вибрации и постоянные изгибания шлангов.
Для шлангов большего диаметра можно подобрать широкий спектр решений: от простого штуцера-ёлочки с закреплённым на хомуте шлангом до быстросъёмных штуцеров, поворачивающихся для компенсации движений узлов станка. Здесь действует простой принцип: если одна и та же прессформа установлена месяцами, то можно и хомутами закрепить шланг (за исключением случаев, когда такое подключение приводит к деформации при работе), а если вы постоянно меняете оснастку, то можно «разориться» и на качественное удобное быстросъёмное решение.
Что касается изгибов шлангов и пространства для их подключения, то эти понятия вытекают одно из другого. Типичный отрицательный пример такой взаимозависимости: когда коллектор для подключения шлангов находится сбоку от плит, а штуцеры прессформы выходят вниз. В этом случае, особенно если шлангов много, их приходится неудобным образом изгибать, да ещё так, чтобы они не мешали друг другу и не деформировались от хода плит и/или хода каретки. Эта возня, безусловно, занимает много времени.
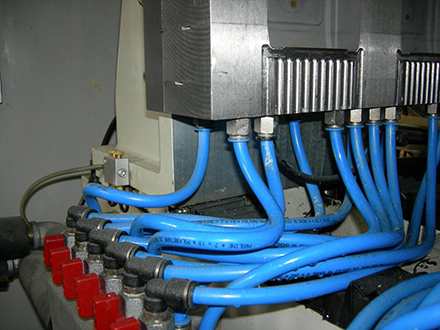
Путь и повороты шлангов с охлаждающей водой должны быть рассчитаны таким образом, чтобы при отключении/подключении их достаточно было просто отбросить в сторону, а потом легко подтянуть. При этом, чтобы не надо было каждый раз думать как их изогнуть для предотвращения изломов от движений станка. Обычно соответствующие шланги (это касается и гидравлических) должны быть U-образно изогнуты параллельно оси движения соответствующего узла станка.
Некоторые производители экструзионно-выдувных машин (как минимум, две немецкие компании) предлагают осуществлять подвод охлаждения через плиты узла смыкания станка так, чтобы непосредственно в задней поверхности прессформы были предусмотрены отверстия для входа/выхода воды и в той же самой позиции на машинной плите ответные отверстия, через которые и идёт водопоток. Т.е. никаких штуцеров вообще, а просто кольцевые уплотнения вокруг отверстий.
Для оценки этой концепции можно вернуться на несколько абзацев назад туда, где мы обсуждали альтернативные замки для крепления прессформ вместо классических болтов. Система удобная, но усложняет унификацию прессформ из различных источников, а также генерирует риски проникновения воды в непредусмотренные для этого узлы машины и оснастки.
Воткнуть четыре быстроразъёмных штуцера, в конце концов, тоже не занимает много времени.
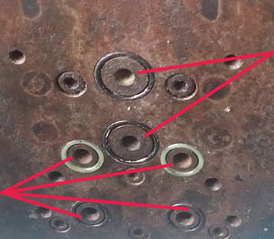
2. Удерживающие и обрубочные маски
Если мы говорим о машинах/прессформах с системами автоматического удаления облоя (а это большинство современных применений экструзионно-выдувного формования), то следом за установкой прессформы встаёт вопрос крепления компонентов этих систем, а это:
- Удерживающие маски (holding masks)
- Обрубочные маски (punching / deflashing masks)
- Захваты извлечения (take out grippers)
2.1 Удерживающие маски
Задача удерживающих масок — захватить изделие, повисшее на выдувном дорне, в то время как каретка находится под головкой, и перенести его в позицию удаления облоя вместе с возвратом каретки под выдувной дорн.
Есть две концепции монтажа удерживающих масок: к машинному кронштейну (прикреплён к плитам станка), или к кронштейну самой прессформы (прикреплён к телу прессформы).
Поскольку почти любая экструзионно-выдувная машина в базовой конфигурации имеет в комплектации кронштейн для удерживающих масок, очень многие пользователи автоматически соглашаются использовать такое стандартное решение. Это означает, что процесс монтажа прессформы и монтажа масок становятся раздельными процессами, и в результате общее время смены формата удлиняется.
Маски ведь надо не просто прикрутить к кронштейну, а ещё и отцентровать их расположение относительно правильной позиции захвата флакона. За редкими исключениями конструкция крепления удерживающих масок включает проушины, а не фиксированные резьбовые отверстия, поэтому при каждой смене прессформы надо снова и снова проводить эту калибровку.
Мы рекомендуем конструировать (заказывать) прессформу с уже интегрированными с ней кронштейнами с удерживающими масками. Оптимальная позиция захвата флакона масками находится на ровно том расстоянии от позиции смыкания, на которое перемещается каретка горизонтально или горизонтально + вертикально (для машин с диагональным ходом каретки), это расстояние известно заранее, поэтому нет проблем спроектировать кронштейн правильным образом, чтобы маска сжимала флакон в нужном месте без всяких центровок и калибровок. Если всё сделано правильно, то монтаж удерживающих масок занимает 0 минут.
Автор в своё время имел спор с инженером одного производителя экструзионно-выдувной упаковки, утверждавшего, что невозможно на стадии проектирования прессформы рассчитать точно правильное положение захвата флакона масками так, чтобы маски гарантировано сжимали его без деформации. Здесь стоит сказать, что, во-первых, бывают исключения и специфические флаконы в т.ч. с повышенными требованиями к качеству поверхности, а, во-вторых, возможны комбинированные решения, где кронштейн всё равно прикреплён к телу прессформы (и монтируется вместе с ней), но есть возможность регулировки положения деталей, контактирующих с изделием (в этом случае центровка масок потребуется, но лишь при самой первой установке).
Группа изделий, где наверняка не получится на чертежах рассчитать положение ёмкости для захвата масками, это евроканистры с утопленными ручками и раскрытием прессформы в двух направлениях. Такие канистры перемещаются по выдувному дорну в процессе извлечения из прессформы, поэтому финальное положение изделия по вертикальной оси можно определить только после испытаний. Тем не менее, и здесь можно сконструировать кронштейны и маски таким образом, чтобы регулировку пришлось осуществлять только при первой установке.
2.2 Обрубочные маски
Обрубка облоя для большинства упаковочных изделий подразделяется на верхний и нижний контур. Горловой и плечевой облой, а также облой в ручках относятся к верхнему, а донный облой к нижнему. В специфических дизайнах изделий могут применятся особые конструкции масок, но мы остановимся на более или менее стандартных решениях.
Актуаторы (т.е. пневматические или гидравлические цилиндры) срубки могут располагаться в стационарной позиции на раме машины, а могут быть прикреплены к каретке и перемещаться вместе с ней. Во втором случае актуаторы есть смысл закреплять на кронштейнах удерживающих масок прессформы, что делает всю конструкцию из прессформы и компонентов для удаления облоя единой системой, которая устанавливается и снимается с машины вместе, а значит без дополнительного затраченного времени. Впрочем, иногда такая конструкция становится слишком громоздкой и затрудняет установку в сборе и/или слишком дорогой, чтобы проектировать её на каждую отдельную прессформу.
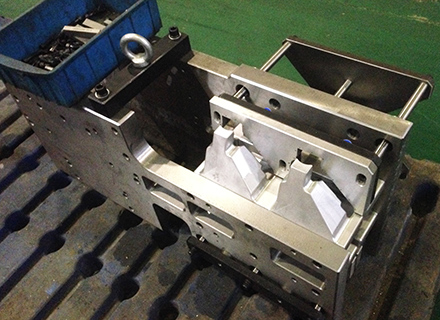
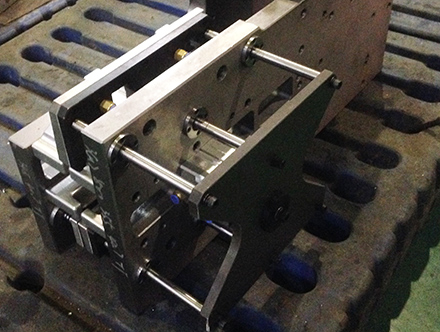
Более классическая компоновка экструзионно-выдувной машины предполагает, что верхняя обрубочная маска прикрепляется к независимому от прессформы актуатору станка. Как и в случае с удерживающими масками обрубочная часть требует подгонки (калибровки) в горизонтальной и вертикальной осях под действительное положение изделия (иногда и в третьей оси). В зависимости от точности и детальности доступных чертежей станка можно с разной степенью успеха рассчитать положение обрубочной маски на стадии проектирования, однако в некоторой подгонке по месту нет ничего страшного.
Важно, чтобы эту калибровку не приходилось делать каждый раз при установке прессформы. Для этого финальная пластина крепежа маски, контактирующая с монтажной пластиной актуатора, не должна содержать никаких проушин, а иметь единственно возможную позицию крепления. Маска может быть очень тяжёлой, и очень часто один человек не может одновременно и держать и прикручивать её к монтажной пластине. Привлечение дополнительного человека — это дополнительные трудовые и временные затраты, поэтому применяются простые механические решения, чтобы маску можно было сначала навесить, освободить руки а затем затягивать болты (например, крепёжные отверстия ключевой формы с расширением верхней части под проход головки болта).
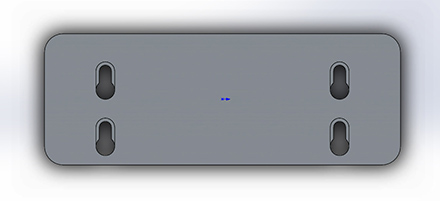
Нижняя обрубочная маска для стандартных изделий — это прямоугольная пластина на актуаторе с ответной подпружиненной пластиной. Перенастройка под различные изделия сводится к регулировке положения пластин по вертикальной оси. Насколько быстро и удобно это делается зависит от конструкции конкретной экструзионно-выдувной машины и прессформы. Нижний обрубщик может двигаться вверх/вниз по пазам и/или иметь набор фиксированных отверстий для крепления на разной высоте, или нижний обрубщик может быть частью прессформы и/или крепиться к плитам смыкания.
2.3 Извлечение изделия
В двух вариантах исполнения системы извлечения изделия из экструзионно-выдувной машины при смене формата (почти) не нужно менять никакие части:
- Выталкивание изделий по направляющим за счёт хода каретки
- Выем изделий 2-осевыми горизонтальными захватами, где для контакта с флаконом используются «мягкие» плоские лапы
В первом случае необходимо сдвинуть/раздвинуть направляющие под новый флакон, а также поднять/опустить нижние подставки, по которым «выезжает» изделие. Во втором случае в зависимости от различий между предыдущим и новым изделием может потребоваться регулирование высоты точки захвата.
Стоит отметить, что принцип выталкивания невозможно комбинировать с исполнением нижней обрубки с перемещающимся за кареткой актуатором — только стационарная нижняя обрубка. Также подобный метод извлечения будет нестабильным для неустойчивых изделий (например, длинных узких флаконов).
Если применяются захваты с присосками или фигурные механические захваты (с выточкой под конкретную геометрию флакона), то форматные части следует делать легко и быстро заменяемыми. Например, в случае присосок не менять каждую головку по одной, но и не снимать целиком всю лапу с кучей механических и пневматических соединений. Наиболее правильно предусмотреть сменные пластины с предустановленными присосками с одной точкой подхода воздуха на всю пластину. Правильное положение присоски на конкретной пластине можно отрегулировать один раз при первой установке, и затем при штатной работе не расходовать на наладку временной ресурс.
Аналогичная рекомендация распространяется и на системы извлечения П-образным движением через верх к центру машины. Форматные части должны быть исполнены сменными блоками под каждое изделие. Если горловины между изделиями одинаковые и захват сделан по принципу расширяющейся внутри горловины «клешни» или шара, то пластины с форматными частями может и не обязательно менять, но должны быть чёткие насечки по регулированию их положения относительно флакона.
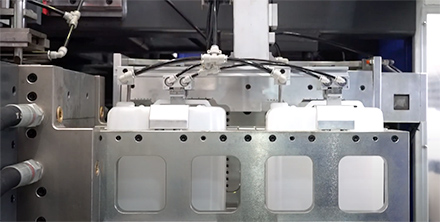
Не забываем и о таком продолжении станка, как конвейерные системы по транспортировке изделий (в точку упаковки или на линию розлива), что особенно актуально для двухстанционных машин. Если изделия сильно разнятся по высоте, то и система с выталкиванием, и система с горизонтальным 2-осевым захватом может потребовать регулирования высоты всей конвейерной ленты. Для длинных конвейеров это может стать довольно трудозатратной статьёй.
Решают проблему как раз системы с П-образным извлечением к центру машины, если вертикальная ось управляется сервоприводом. Тогда точку отпускания флакона можно отрегулировать под каждое изделие и записать в память машины. Или горизонтальные системы извлечения, но 3-х осевые, так чтобы было настраиваемое по длине хода вертикальное движение.
3. Выдувные дорны
К калибровочной станции с выдувными дорнами не прикасаются в случае, если у изделия не только точно такая же горловина, но и расположена она в том же месте флакона (по центру), и прессформы с точки зрения горловых частей сконструированы одинаково. Во всех остальных случаях калибровочная станция также подлежит перенастройке хотя бы для смещения точки опускания дорнов.
Можно выделить четыре степени глубины перенастройки калибровочной станции:
- Перемещение всей станции влево или вправо (без вмешательства в дорны)
- Смена наконечника выдувного дорна и обрезного кольца
- Смена выдувного дорна целиком
- Смена блока выдувных дорнов
В калибровочной станции есть прямая зависимость размера бюджета на форматные части и времени, затрачиваемого на переналадку.
Так, наиболее быстрой является смена т.н. блока выдувных дорнов (blow pin block). В этом случае меняется вся пластина с размещённым внутри неё коллектором распределения охлаждающей воды и воздуха на все дорны и с прикреплёнными к ней самими выдувными дорнами, которые уже откалиброваны под прессформу. Блок, конечно же, должен иметь фиксированную точку крепления к калибровочной станции, т.е. его нельзя установить неверно. Один раз отстроенный под прессформу блок при снятии и переустановке вернётся в то же отстроенное положение.
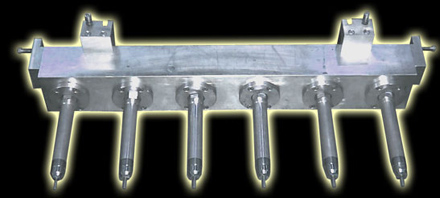
Таким образом, время переналадки калибровочной станции будет равно времени механических работ по замене блока (они разнятся в зависимости от габаритов и конструктива конкретной машины/прессформы), но, что важнее, исключается процесс повторной настройки (центровки) выдувных дорнов, всегда влекущий за собой риски ошибок и повреждений оснастки.
К слову, для получения эффекта от применения блоков выдувных дорнов центровка прессформы при креплении к плитам должна также выполнятся по системе пазов и направляющих (описано выше). Проще говоря, и блок выдувных дорнов, и прессформа каждый раз должны вставать в одну и ту же позицию по горизонтальной и вертикальной осям.
Более бюджетное решение — смена самих выдувных дорнов. Наиболее хорошо такая концепция работает, когда отдельно взятые дорны в сборе снимаются и устанавливаются быстро и легко. Некоторые производители, например, используют цанговый принцип крепления, и это позволяет буквально за пару минут поменять набор из 4–6 дорнов, и ещё за пару минут воткнуть в них воду и воздух.
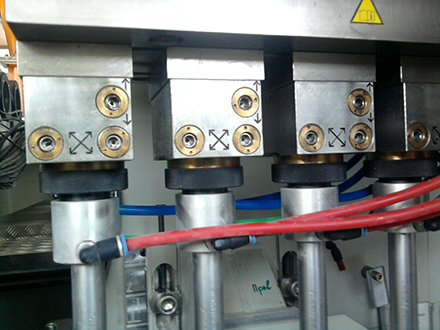
Жирный минус такого решения — при каждой переналадке необходимость подгонки положения выдувного дорна под точку захода и центровка по гнезду.
Ещё более бюджетное решение — замена только наконечника выдувного дорна и обрезного кольца. Если крепление выдувных дорнов сделано неудобно, то замена наконечника с кольцом может быть не столько дешевле, сколько просто быстрее, чем замена дорна в сборе. Но возможность изменения только кольца и наконечника в рамках одного и того же корпуса доступна лишь в определённых рамках разброса диаметров горловин. Если диаметры горловин двух флаконов слишком сильно отличаются, то в любом случае придётся менять дорн в сборе.
Предположим, что у двух изделий одинаковая горловина, одинаково сделана горловая часть прессформы, но в одном случае она находится по центру, а в другом — с края флакона. Дешёвым решением будет просто перемещение всей станции влево или право, но тогда придётся подбирать правильную позицию калибровки и, скорее всего, заново центровать дорны. Эффективным решением будет применение блока выдувных дорнов либо раздельного на каждую из двух прессформ, либо (если это технически возможно в конкретном случае) одного и того же, но со второй точкой фиксированного крепления для второй прессформы.
Особняком стоит переход с флаконов с наклонной горловиной на обычные и обратно. Здесь невозможно обойтись какими-то быстросъёмными решениями и придётся долго возиться с поворотом и заменой компонентов калибровочной станции, а затем с центровкой. Если есть возможность разбить производство флаконов с наклонной горловиной и обычных по разным станкам, то мы настоятельно рекомендуем именно так и поступать.
4. Фильеры
В некоторых случаях между изделиями сохраняется одинаковый рукавообразующий инструмент (фильера), например, линейка круглых флаконов без плечевого облоя в диапазоне 100–300 мл вполне может это допускать. Но очень часто и фильеры становятся форматной частью, подлежащей смене при переходе на другую прессформу. С точки зрения временного фактора здесь надо учесть две особенности.
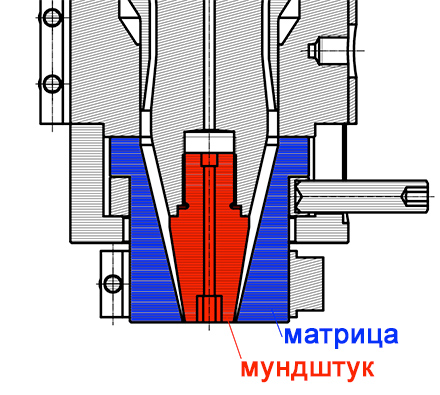
Во-первых, фильеры снимаются и устанавливаются только «на горячую» (т.е. при прогретой головке), и после извлечения перед отправкой на склад оснастки обязательно требуют тщательной отчистки рабочих поверхностей от остатков полимера посредством латунного скребка. Отчистка должна быть завершена пока металл ещё не полностью остыл, соответственно её приходится начинать сразу, что не позволяет одному и тому же человеку без промедления устанавливать на станок фильеру на новое изделие (он занят чисткой). Требуется или ещё один человек, или ожидание последовательности процессов.
Во-вторых, каждый раз когда устанавливается новая фильера, её матрицу (стакан) нужно заново центровать в горизонтальной плоскости дабы получить равнотолщинный рукав без изгибов.
За исключением особо малых головок для извлечения мундштука и матрицы фильеры приходится в т.ч. снимать нижний нагреватель и отключать термопару, и эти процессы, включая описанные выше этапы чистки и центровки, по временным затратам кратны количеству ручьёв головки без какой-либо возможности оптимизации.
Иногда производители выдувной тары готовы идти на некоторые компромиссы по технологичности выдува и унифицировать большее количество фильер между разными изделиями. Это происходит как осознанно, так и не осознанно. Типичный пример такой ситуации, когда для какого-то сильно плоского флакона или канистры используется круглая фильера (а не овализированная) только потому, что другие изделия на этом же станке уже «нормально идут» на круглой.
Кстати, в некоторых случаях наличие паризон-контроля на станке позволяет унифицировать больше фильер между изделиями. Так, при большом коэффициенте раздува (выдув широкого изделия из узкого рукава) под горловиной флакона с внутренней стороны, а также на дне скапливаются излишки массы (из-за того, что рукав имеет очень большую толщину стенки и ему некуда деваться), здесь за счёт паризон-контроля мы частично можем ликвидировать эти паразитические утолщения. Без паризон-контроля для хорошего распределения массы на том же флаконе потребовался бы широкий рукав (другая фильера) и облой на плечах.
5. Экструзионная головка
Выше уже вскользь упоминалось, что любые перенастройки, связанные со сменой экструзионной головки (изменение количества ручьёв), являются длинными и трудоёмкими.
Следует специально подчеркнуть, что компоновку изделий на экструзионно-выдувных машинах лучше делать так, чтобы количество ручьёв менять не приходилось.
6. Настройки машины
Предположим, мы поменяли все требуемые форматные части оснастки, что ещё надо сделать для запуска производства на новом изделии? Конечно же, изменить настройки и регулировки станка.
Технологический процесс в экструзионно-выдувной машине регулируется следующими группами настроек:
- Температуры экструдера и головки
- Таймеры (задержки и длительности)
- Давление выдувного воздуха
- Давление воздуха поддува рукава
- Центровка рукава
- Профиль толщины рукава
- Профили скорости и хода устройств
Когда мы находим правильный технологический рецепт для того или иного изделия, логичным будет записать все найденные параметры и воспроизводить их каждый раз при установке соответствующей прессформы. Однако, в экструзионно-выдувной машине некоторые настройки остаются механическими, поэтому их придётся «отловить» заново. Речь идёт, как минимум, о давлениях воздуха поддува рукава и центровке рукава (т.е. центровке фильеры, о которой говорилось выше).
Но на самом деле в зависимости от степени технической продвинутости станка механическими настройками могут быть также давление выдувного воздуха (очень часто), профиль толщины рукава (в отсутствие паризон-контроля) и профили скорости/хода устройств (если соответствующая ось управляется не пропорциональной гидравликой или сервоприводом). Последнее особенно актуально для оси хода выдувного дорна, с которой обычно надо много возиться для поиска оптимальной точки останова и скорости подвода. В некоторых станках (как правило, более старых) управление температурами остаётся электронным, но вынесено за пределы главной панели во внешние терморегуляторы по зонам.
Отдельно стоит сказать про управление профилем толщины стенки на лету, т.е. о паризон-контроле. Во многих азиатских экструзионно-выдувных машинах распространённой практикой является вынос этого контура в отдельную панель (обычно серии Moog Digipack). В этом случае управление профилем рукава остаётся электронным и записываемым в память, но с прикладной точки зрения оно отвязано от остальных параметров управления машиной. В полноценных машинных контроллерах (включающих регулировку паризон-контроля в основной панели) профиль не только записан технически в тот же рецептный файл, но и зачастую интегрирован с другими настройками, например, очень удобно задавать точку перехода на второе давление поддува рукава (при использовании запайки рукава) не по таймеру, а по точке профиля.
Для быстрой смены формата желательно иметь записанный в панели управления станка единый файл рецепта, который сразу загрузит максимальное количество параметров, подлежащих оцифровке. В идеальном случае это будет всё кроме воздуха поддува рукава и центровки фильер.
***
За годы работы мы очень часто слышали от новичков отрасли вопрос «сколько закладывать времени на смену прессформы». Правильным ответом на него обычно являлась целая лекция о том, от скольких параметров и нюансов зависят соответствующие трудозатраты, и что необходимо делать для их сокращения. Чтобы не повторять эту лекцию снова и снова пришлось написать данную статью.
Мы призываем с осторожностью относиться к рекламным видео производителей машин, где показывают смену прессформы за 16 минут, 19 минут и т.д. Ни на одном из таких видео не показан полный процесс, включая смену фильер, центровки и т.п., и всегда работу на них выполняют инженеры завода-изготовителя, идеально тренированные и не расходующие ни секунды времени в холостую (т.е. в стерильных условиях, которых никогда не бывает на настоящем заводе).
С похожим скепсисом предлагаем относится к любым усреднённым декларациям о том, что смена формата занимает столько-то минут или столько-то часов.
Для ответа на этот важнейший вопрос в первую очередь нужно проанализировать, что за оснастка будет меняться, какие технические средства есть (планируются) на предприятии, и даже в этом случае спрогнозировать время смены формата будет невозможно (если мы говорим о начинающем в выдуве предприятии). Первые смены будут происходить мучительно долго, после месяцев работы – быстрее, с годами — ещё быстрее.
Пример из практики автора: около 10 лет назад мы запускали экструзионно-выдувную машину с несколькими прессформами в одном сибирском городе, и для предприятия это был уже второй такой станок. В тех условиях, что были предоставлены, наш инженер в процессе пуско-наладочных работ менял прессформы за 5–6 часов. Казалось бы, ничего особенного. Но местные наладчики были не очень довольны, т.к. по устоявшемуся там регламенту, согласованному с начальством, им на такую работу отводилось 2 дня («с чувством, с толком, с расстановкой»), и теперь прямо на глазах у руководства оказалось, что работу можно выполнять гораздо быстрее. Неудобная получилась тогда ситуация перед мужиками.