Во второй части гида продолжаем обзор выдувных полимеров, здесь речь пойдёт о более редких (для этого метода переработки) видах.
№3 — ПВХ (Поливинилхлорид, по-английски — Polyvinylchloride, кратко PVC)
Один из самых крупнотоннажных пластиков по общему потреблению когда-то и в выдувном формовании применялся весьма активно. Сейчас это трудно представить, но в 1970/80-х годах ПВХ был основной опцией при необходимости получить бутылку с прозрачными стенками, и в ПВХ-ёмкости упаковывалось и, например, подсолнечное масло, и напитки, и соусы. Ещё бы, ведь ПВХ не только полностью прозрачен, но и обеспечивает хорошие и довольно универсальные барьерные свойства бутылки.
Затем, появление альтернативных материалов (таких как ПЭТ), а также борьба за экологию (у ПВХ и готовой тары из ПВХ есть трудности с переработкой) привели к сокращению использования ПВХ в выдувном формовании, что уменьшило спрос, а значит и предложение по сырью на рынке, сделав его менее доступным, что в свою очередь ещё больше сузило круг применений.
ПВХ / Применения
Более или менее везде ПВХ уже давно запрещён для производства пищевой тары из-за проблем при вторичной переработке (при горении и/или сильном нагреве ПВХ выделяет опасные хлористые вещества), но ещё в 1990-х и даже 2000-х годах этот полимер оставался «в ходу» в таких сферах как косметические и фармацевтические флаконы. В этот период ПВХ был незначительно дороже ПЭТ, но при этом (в 1,5–2 раза) дешевле ПЭТГ, поэтому для экструзионно-выдувных ёмкостей со сложной геометрией, нестандартными горловинами и малыми тиражами он оставался актуален.
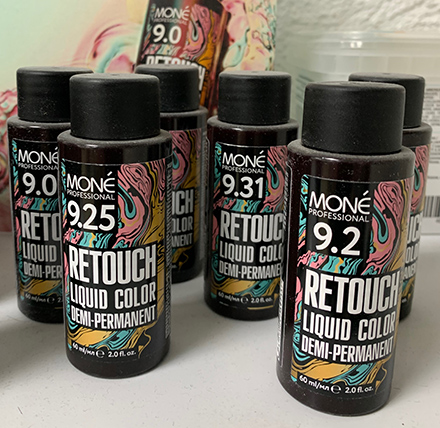
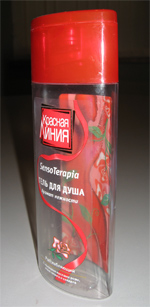
Сегодня, когда купить выдувной ПВХ уже практически негде, а экологическое лобби достигло пика, этому полимеру осталось сугубо нишевое узкое применение. Так, благодаря специфическим барьерным свойствам, ПВХ-флаконы можно обнаружить в упаковке некоторых видов химических средств для работы с окрашиванием волос. Также, по крайней мере до недавнего времени, продолжали встречаться некоторые медикаменты в ПВХ-флаконах, но это во многом связано с инерционностью (медлительностью) внедрения изменений в фармацевтической отрасли, где для замены упаковочного материала требуется очень много усилий и воли, а также в любом случае много времени и испытаний (поэтому «проще» продолжать и продолжать использование проверенных материалов до тех пор пока это ещё технически возможно).
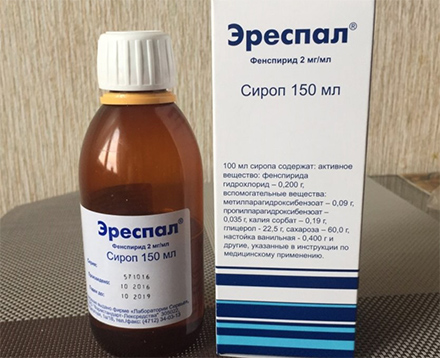
ПВХ / Переработка
Выдувную тару из ПВХ можно производить следующими технологиями:
- Экструзионно-выдувное формование
- Инжекционно-выдувное формование (IBM) *
* — По большому счёту единственной технологией, которой подвластно производство ёмкостей из ПВХ — это экструзионно-выдувное формование, однако с большими ограничениями и только на определённых станках автору известен успешный опыт производства ПВХ-флаконов на инжекционно-выдувных машинах без продольной вытяжки преформы (IBM-технология).
Материал капризный и термочувствительный. Основная особенность — при малейшем застое под высокой температурой начинает гореть. Поэтому одним из главных условий в подготовке экструзионно-выдувной машины является обеспечение хорошей и при этом мягкой динамики потока расплава на всём его пути от гранулы до выхода из экструзионной головки в сочетании с чётким температурным контролем на всех стадиях.
Поскольку в «старые времена» едва ли каждая вторая или третья экструзионно-выдувная машина предназначалась для переработки ПВХ, то у производителей исторически сформировался определённый пакет особенностей станка для данного полимера. Такой пакет мы для простоты называем ПВХ-исполнением, и вот что обычно туда входит:
- Шнек с малыми сдвиговыми усилиями и без смесительных зон. В идеале в центре оси шнека должен быть предусмотрен контур для его термостатирования с помощью масла (для возможности регулирования температуры шнека изнутри).
- Масляная рубашка охлаждения (управляемая посредством термостата) вокруг ствола вместо традиционных вентиляторов охлаждения.
- Экструзионная головка торпедного типа (подача материала сверху по центру) с максимально сглаженным (большой радиус скругления) переходом потока из горизонтальной оси в вертикальную.
- Отсутствие любого рода фильтрации расплава.
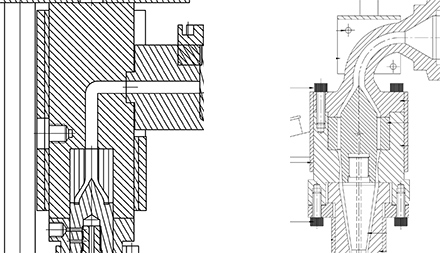
Несмотря на дефицит современных задач по производству изделий из ПВХ, опция «ПВХ-исполнение» для экструзионно-выдувной машины остаётся важной, т.к. другие термочувствительные материалы, такие как ПЭТГ и сополиэфиры ПЭТ (о которых говорили ранее) или поликарбонат (о котором поговорим далее) гарантированно перерабатываются на станке как раз в т.н. ПВХ-исполнении.
№4 — ПЭВД (Полиэтилен высокого давления, он же полиэтилен низкой плотности, обозначается ПЭВД или ПВД или ПЭНП, по-английски — Low Density Polyethylene, кратко LDPE или PE-LD)
Обсуждение ПЭВД в выдувном формовании можно считать продолжением или дополнением темы выдува ПЭНД. ПЭВД — менее плотный и более мягкий и эластичный вариант полиэтилена, что предоставляет дополнительные возможности во всевозможных применениях.
ПЭВД / Применения
В смеси с ПЭНД. В выдувном формовании ПЭВД может смешиваться с ПЭНД в различных пропорциях и тем самым обеспечивать изделию следующие свойства:
- Сварные швы экструзионно-выдувных изделий становятся более прочными на разрыв благодаря эластичному (склеивающему) характеру материала ПЭВД.
- Швы экструзионно-выдувных изделий также могут лучше противодействовать растрескиванию при фасовке некоторых видов содержимого (может касаться бытовой химии, но не только).
- Изделие легче сдавливается руками, что иногда необходимо.
Последнее, к сожалению, означает одновременно и то, что ёмкость с содержанием ПЭВД выдерживает меньшие прочностные нагрузки (в первую очередь top load), а значит общий вес приходится увеличивать, что с учётом более низкой плотности ПЭВД, добавляет сырьевые затраты. Поэтому ПЭВД есть смысл использовать исключительно при наличии явной причины.
Пример из практики автора: время от времени встречаются переработчики с сильно устаревшим (древним) экструзионно-выдувным оборудованием, где ПЭВД добавляют просто для обеспечения стабильности экструзии при использовании дроблёнки. При переходе на современное оборудование таким компаниям мы рекомендуем пересмотреть композицию сырья и ещё раз подумать (или проверить) действительно ли в их флаконе нужен ПЭВД.
В зависимости от изделия содержание ПЭВД варьируется обычно от 20 до 50%.
В чистом виде. 100% ПЭВД используется реже чем смесевой вариант с ПЭНД, однако и такие применения существуют. Как правило, это изделия, требующие большой эластичности (сжимаемости). Здесь можно вспомнить примеры из нашей статьи о дизайне экструзионно-выдувных ёмкостей.
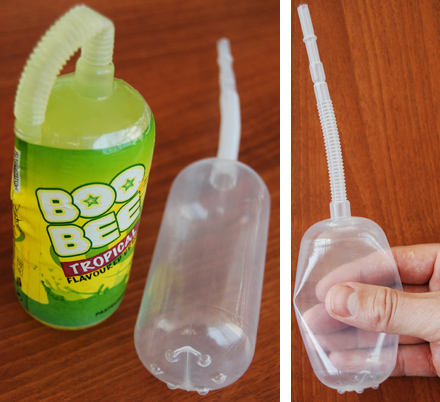
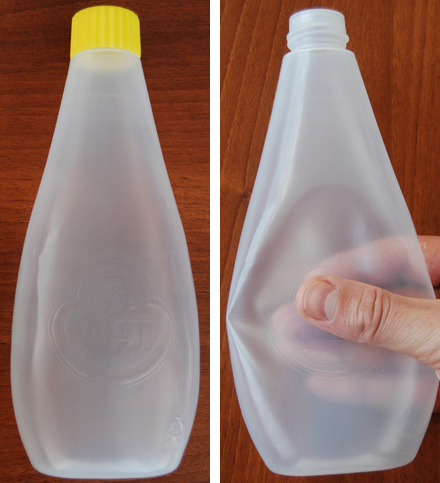
Капельные флаконы вместимостью 5–20 мл также чаще всего сделаны из 100% ПЭВД, т.к. при малом размере ёмкости смесевой вариант ПЭНД/ПЭВД всё равно получается слишком жёстким, и флакон в руке трудно сжимается для выдавливания лексредства через отверстие капельника.
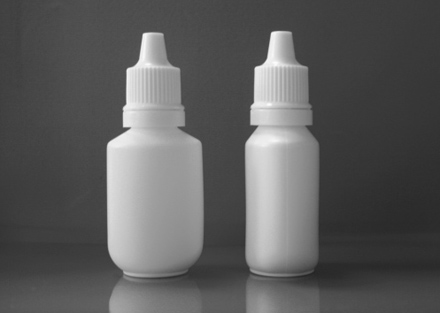
ПЭВД / Переработка
Выдувную тару из ПЭВД можно производить следующими технологиями:
- Экструзионно-выдувное формование
- Инжекционно-выдувное формование (IBM)
- Инжекционно-выдувное формование с вытяжкой (ISBM) *
При экструзионно-выдувном формовании ПЭВД используется идентичная спецификация оборудования как и для ПЭНД. Отличия в переработке прямо следуют из свойств материала, который является более мягким по сравнению с ПЭНД, поэтому ниже становятся и температуры и, например, требования по усилию на пережатие обрезной кромки.
Для технологии IBM ПЭВД представляется во многом даже более типичным сырьём нежели ПЭНД, т.к. этот метод переработки преимущественно и используется для изготовления маленьких капельных флаконов, где материал ПЭВД как раз востребован.
Что касается ISBM, то звёздочку в списке поставили из-за продолжающегося на момент публикации этой статьи освоения применений различных видов полиэтилена на инжекционно-выдувных машинах с вытяжкой и в т.ч. в работе с полиэтиленами высокого давления (наибольшие усилия в этой сфере делает компания Aoki).
Смесевые флаконы ПЭВД/ПЭНД технологией ISBM от Aoki уже производятся промышленно в некоторых странах. Если стоит задача производства из 100% ПЭВД, то перед запуском проекта необходим выбор и тестирование конкретных марок сырья для проверки совместимости и технологичности.
№5 — ПП (Полипропилен, по-английски — Polypropylene, кратко PP)
Полипропилен вместе с полиэтиленами составляет большой класс полимеров, называемый полиолефинами. Эти виды сырья сгруппированы из-за схожести происхождения и свойств. ПП на самом деле третий по популярности выдувной полимер, но с огромным отставанием от большой двойки ПЭТ/ПЭНД.
ПП / Применения
В части выдувного формования ПП по сравнению с полиэтиленами почти всегда чуть-чуть дороже и чуть-чуть сложнее в переработке, поэтому при прочих равных при выборе материала для изделия останавливаются на ПЭ. За исключением ряда применений, где есть требования, которые ПП может удовлетворить, в то время как ПЭ — нет. Вот какие это могут быть требования.
Прозрачность. Как обсуждалось в первой части, полиэтилен имеет серый мутный цвет и практически не прозрачен (можно видеть только уровень жидкости). Полипропилен, в свою очередь, обладает прозрачностью разной степени, которая зависит от марки сырья, модификации добавками (в статье о прозрачной барьерной пищевой таре рассказывали как работают т.н. «осветлители» ПП), а также от метода переработки, толщины стенки и от того продукта, который налит в ёмкость (так, содержимое сплошного насыщенного цвета будет видно почти без «потерь»).
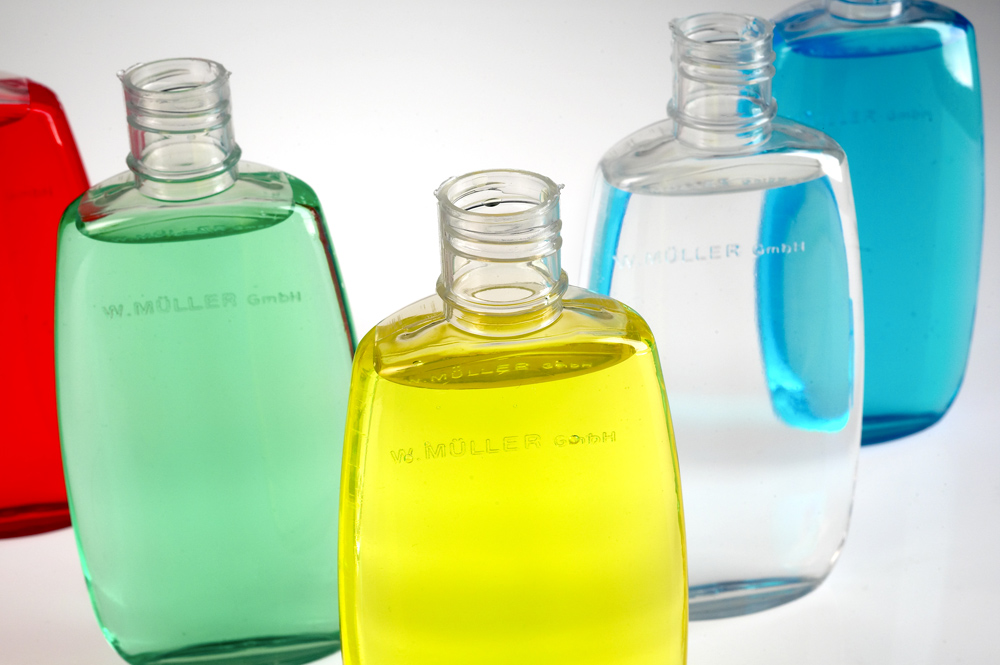
Примечание: Полипропилен не обладает полной кристальной прозрачностью как ПЭТ или даже ПВХ и всегда остаётся некоторая мутность, которая обозначается термином Haze и часто является частью технической спецификации материала и указывается в процентах (измерение обычно на пластине толщиной 1 мм).
За счёт своей неплохой прозрачности при разумной цене и возможности перерабатываться экструзионно-выдувным формованием ПП в ряде применений конкурирует с ПЭТ (например, в косметике и бытовой химии). К сожалению, если говорить конкретно о российском рынке, то проблема заключается в отсутствии постоянного и доступного предложения по семейству выдувных рандом-сополимеров, которые являются наиболее прозрачными видами ПП и которые где-то могли бы полноценно заменить ПЭТ.
Российские выдувные рандом-сополимеры ПП то есть, то нет, что сами производители сырья объясняют низким спросом. Импортные прозрачные марки ПП имеются в достатке, но их итоговая стоимость и получающаяся слишком большая разница с ПЭТ приводит к тому, что используется этот материал в довольно узком спектре задач. Обычно только там, где ПЭТ в принципе не подходит (канистры с ручкой или флаконы экстремально сложной геометрии).
Классический ПП марки 030 российских заводов доступен всегда, но по степени прозрачности он, конечно, не слишком впечатляет (хотя разница с ПЭНД, безусловно, огромная).
Температурная стойкость. Обсуждая ПЭНД, мы уже касались темы стойкости полученной тары к температурному воздействию и выяснили, что полиэтилен весьма неплох в этом отношении по сравнению с ПЭТ. Но полипропилен, если мы говорим о высоких температурах, ещё лучше, чем ПЭНД, и это очень важная особенность, благодаря которой ПП становится предпочтительным материалом в тех или иных проектах.
Ёмкости из ПП могут выдерживать температурное воздействие на уровне 120–130 градусов (поведение тары во время и после воздействия, при этом, будет зависеть от ряда конкретных условий и факторов). Такой температурный порог имеет ключевое значение, т.к. в этот диапазон укладываются основные виды стерилизации, а значит есть возможность обеспечить выпуск стерильных ёмкостей или стерилизовать содержимое прямо вместе с тарой (актуально для медицинской и пищевых отраслей).

И, конечно, ПП-тара значительно лучше подходит для разных видов горячего розлива, хотя и стоит помнить, что деформация тары при горячем розливе происходит не только (и не столько) от размягчения пластика от контакта с чем-то горячим, сколько от силы вакуума, образующегося внутри бутылки после остывания продукта и уменьшения его в объёме (последствия температурного расширения).
Справедливости ради надо отметить и поведение ПП-ёмкостей при отрицательных температурах (морозостойкость), ведь здесь полипропилен значительно проигрывает не только ПЭНД, но и даже ПЭТу. Флаконы и бутылки, наполненные продуктом, на морозе имеют повышенную возможность растрескаться при падении на твёрдую поверхность вследствие большой хрупкости полипропилена в этих условиях. Частично эту проблему можно решить морозостойкими добавками, но это не 100% панацея.
Резюмируя применения полипропилена, можно кратко заключить, что данный полимер используется вместо ПЭНД в тех случаях, когда нужна прозрачность и/или повышенная температурная стойкость, и вместо ПЭТ в тех случаях, когда нужна сложная экструзионно-выдувная геометрия флакона и/или температурная стойкость и/или барьерные свойства полиолефина (например, щелочи или барьер по влаге).
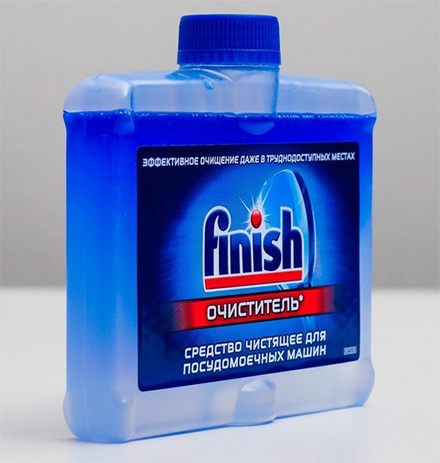
ПП / Переработка
Выдувную тару из ПП можно производить следующими технологиями:
- Экструзионно-выдувное формование
- Инжекционно-выдувное формование (IBM)
- Инжекционно-выдувное формование с вытяжкой (ISBM)
- 2-стадийное выдувное формование
Полипропилен — единственный полимер, который пригоден для получения из него изделий всеми технологиями выдувного формования.
При экструзионно-выдувном формовании ПП не слишком сильно отличается от полиэтилена, есть только некоторые особенности:
- Температуры выше
- Материал более жёсткий по сравнению с ПЭ и усилие на пережатие обрезной кромки требуется примерно на 70% больше
- Пластикация экструдера в кг/ч становится меньше на 20–30%
- Предпочтительнее обрезка рукава прогреваемым лезвием (также как и обрезка фальш-горловин вращением тоже прогреваемым лезвием)
- Можно использовать те же прессформы, но для ПП предпочтительнее полированная поверхность формообразующих, в то время как для ПЭ подходит только пескоструйная
Примечание: иногда можно встретить флаконы с маркировкой HDPE, которые на самом деле изготовлены из полипропилена. Поскольку оснастка от полиэтилена подходит для ПП, то переделывать значки на прессформе в металле обычно никому не хочется. Отличить такие флаконы можно по внешнему виду даже если они окрашены — у ПП поверхность будет более глянцевая, а у ПЭ — матовая.
При инжекционно-выдувном формовании (IBM) переработка ПП отличается от полиэтилена в основном только более высокими температурами, а вот при инжекционно-выдувном формовании с вытяжкой (ISBM) производство изделий из ПП имеет выраженную специфику. Правда при использовании ISBM-технологии сравнивать следует не с полиэтиленом, а с ПЭТ, который для ISBM считается эталонным (основным) видом сырья.
Наиболее сложный момент при ISBM-формовании из ПП — это горизонтальное растяжение горячей преформы в стороны до конечной формы флакона. Внутренние температуры стенок ПП-преформы в разных её местах, в отличие от ПЭТ, варьируются и с трудом стабилизируются, поэтому при растягивании эта преформа с разными температурами в разных точках формирует изделие, у которого толщины стенок также варьируются и также будут иметь большой разброс (что автоматически делает полученную ёмкость некачественной).
Частично решает эту проблему выдержка преформы после стадии литья до начала выдува, чтобы дать температурным вариациям сгладиться, но это не всегда достаточно. Чем больше коэффициент раздува (т.е. разница между диаметром горловины и диаметром тела), тем толще стенки преформы и дольше путь формования и в конечном итоге тем сильнее описанный эффект неравномерного раздува. Поэтому без больших ограничений ISBM-формование из ПП подойдёт лишь для ёмкостей с минимальным коэффициентом раздува, а при большом коэффициенте необходимо сильно занижать толщины стенок.
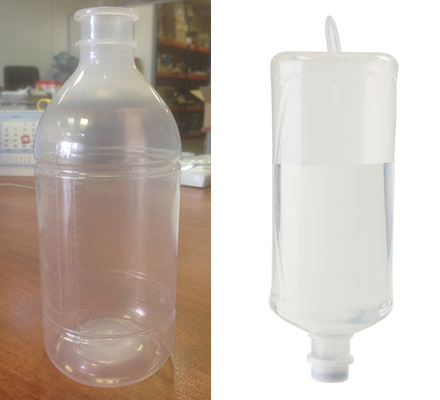
Есть задачи, когда из полипропилена нужно получить изделие с узкой горловиной, большим диаметром тела (т.е. коэффициент раздува большой) и довольно толстыми стенками, пример: бутылки для инфузионных растворов. В этом случае приходится использовать инжекционно-выдувную машину в специальном исполнении, где после литья преформа сначала раздувается до промежуточной формы (грубо говоря, выдувается наполовину), затем каретка переносит эту заготовку в окончательную выдувную прессформу, и только там изделие формуется полностью. Конечно, такой метод и увеличивает цикл и уменьшает количество гнёзд, что драматически снижает общую производительность, а значит удорожает производство. Но, к сожалению, это остаётся единственным вариантом производства некоторых видов выдувных изделий из ПП.
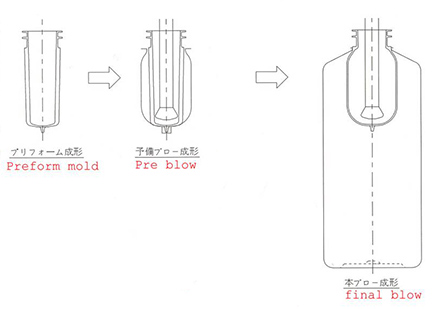
Наконец, что касается отдельного литья преформ на термопластавтомате с последующим независимым процессом их нагрева и раздува (т.е. 2-стадийное выдувное формование), то и такой рынок, пусть и небольшой, но существует. К недостаткам метода относятся все типичные недостатки 2-стадийного процесса в ПЭТе, которые обсуждались нами на вебинаре по ISBM. Только к ним добавляются ещё проблемы с проектированием дизайна преформы и настройки технологического процесса выдува, поскольку знаний и опыта в полипропилене на эту тему гораздо меньше, чем по ПЭТ, и найти правильные технические решения крайне сложно.
№6 — ПС (Полистирол, по-английски — Polystyrene, кратко PS)
Вот мы и добрались до действительно редких в выдувном формовании полимерных материалов. Но, коль скоро начав этот большой гид мы взяли обязательство рассказать про все виды выдуваемого сырья, то игнорировать ни один из них мы не будем.
Мало кто вообще знает, что полистирол используется в выдувном формовании. Недорогой полимер,обладающий прозрачностью (но не все подвиды ПС) и возможностью снижать вес изделий (но не все подвиды ПС), теоретически мог бы обрести популярность в отрасли, но отсутствие большого предложения выдувных марок полистирола у заводов производителей сырья приводит к низкому интересу переработчиков, которые предпочитают для выдува доступные традиционные материалы. При отсутствии реального интереса у переработчиков производители сырья также не видят необходимости активничать в этой сфере, что формирует классический замкнутый круг.
В 2000-х годах один из крупнейших мировых производителей полистирола, концерн BASF, пытался рекламировать и внедрять на рынок некоторые марки ударопрочного ПС (High Impact Polystyrene, HIPS), пригодные в качестве замены ПЭТ для инжекционно-выдувного формования с вытяжкой (ISBM) или 2-стадийного выдувного формования. Акцент был на пищевой отрасли и возможности сокращать стоимость тары благодаря тому, что из ПС она, по расчётам BASF, получается на 20% легче. Но экономический эффект от снижения веса возможен лишь при равенстве цены двух сравниваемых материалов, а с этим у ПС возникли проблемы, и в итоге массовый и доступный везде ПЭТ «переиграл» полистирол, выдувные марки которого кроме BASF по сути никто и не производил.
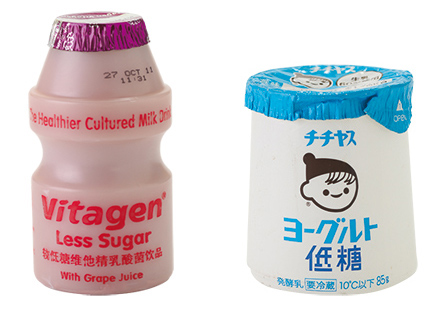
На сегодняшний день определённый рынок выдува есть у ударопрочного полистирола в Азии, где из этого материала инжекционно-выдувным формованием (IBM) и инжекционно-выдувным формованием с вытяжкой (ISBM) производят тонкостенные контейнеры для йогуртов 50–150 мл. В прошлом очень редко, но попадались толстенные флаконы из прозрачного полистирола для медицинских препаратов. Прозрачный полистирол весьма хрупкий и капризный, поэтому в качестве массовой замены таким материалам как ПВХ, ПЭТГ или тем более ПЭТ он не сработал.
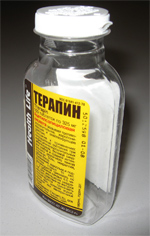
№7 — Другие / Other
Маркировкой «7» OTHER обозначается тара или сделанная из какого-либо материала, не вошедшего в список шести, или из комбинации нескольких материалов (часть из которых может не входить в список шести) — сюда относятся, например, многослойные изделия. Иногда маркировкой OTHER обозначают флаконы из смеси ПЭНД и ПЭВД (хотя оба входят в список шести) или 2-х слойные флаконы, в основном состоящие из ПЭНД, но имеющие тонкий наружный слой из материала типа Soft Touch, хотя этот материал обычно также является производным полиэтилена.
Далее мы поговорим о конкретных видах сырья, обозначаемых цифрой «7».
ПК (Поликарбонат, по-английски — Polycarbonate, кратко PC)
Выдувные изделия из поликарбоната имеют следующие основные свойства:
- Отличная оптическая прозрачность
- Высокая прочность и механическая износостойкость поверхности
- Выдерживают длительную обработку очень высокой температурой
Звучит впечатляющие, но при этом поликарбонат а) очень дорогой б) очень капризный в переработке. Такая комбинация свойств сделала материал востребованным в следующих секторах выдува:
- Детские бутылки для кормления
- Спортивные бутылки
- 19 л бутылки с ручкой для воды в кулерах
- Специальные изделия технического назначения
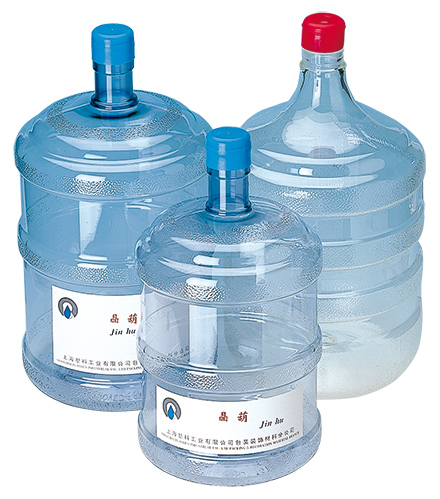
Все описанные изделия — продукты с солидной добавленной стоимостью и многоразового использования; при таких условиях высокая стоимость сырья и его переработки оказывается оправданной.
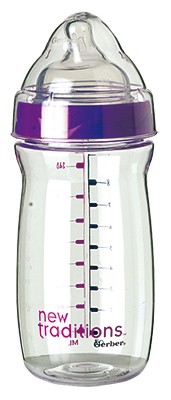
12–15 лет назад известная мировая истерика с Бисфенолом А привела к отмиранию ПК в детском кормлении и спортивных бутылках, что оставило полимеру к сегодняшнему дню только 19 л канистры для воды и технические изделия.
Поликарбонат перерабатывается как экструзионно-выдувным формованием, так и инжекционно-выдувным с вытяжкой и без.
Переработка ПК на экструзионно-выдувной машине несколько отличается от полиэтилена, и вот какие особенности можно выделить (помимо более высоких температур):
- Требуется сушка сырья в горячевоздушной сушилке, а ещё лучше с помощью влагоустранителей аналогично ПЭТ
- Шнек и головка для термочувствительных материалов, например, может подойти ПВХ-исполнение
- При использовании аккумуляторных головок (очень распространено для ПК) требуется соблюсти качество внутренних поверхностей максимально противодействующее налипанию материала и/или образованию застойных зон
- От привода экструдера требуется значительно больший крутящий момент по сравнению с полиэтиленом
- Усилие на пережатие обрезной кромки требуется в два раза больше, чем для полиэтилена
- Поверхность формообразующих — полированная
- Выдувные прессформы охлаждаются не холодной водой, а термостатируются на примерно 60–90 градусах
- После остановки машины требуется полная прочистка от остатков поликарбоната в шнеке или головке
- Добавление более 20–30% измельчённого облоя может привести к появлению желтизны или потемнению (если изделие полностью прозрачное без красителей)
При инжекционно-выдувном формовании особенностей при переработке ПК меньше из-за отсутствия такого технологически сложного этапа как формирование трубчатой заготовки (рукава) в экструзионной головке, отсутствия процесса пережатия кромки и отсутствия дробления облоя. В зависимости от конкретной машины или процесса, на инжекционно-выдувной машине для ПК может быть специальный шнек, а также отличающиеся от ПЭТ или ПЭ технологические режимы.
Поскольку поликарбонатовые технические изделия это, как правило, всё же экструзионно-выдувное формование из-за сложных геометрических форм, то реально оставшееся применение инжекционно-выдувных машин в ПК на рынке — только 19 л бутылки для кулеров.
Тритан / Tritan
Tritan — это не вид полимера, а коммерческое название конкретной марки одного из ПЭТ-сополиэфиров компании Eastman. В отличие от других сополиэфиров, изделия из которых по свойствам весьма похожи на обычные ПЭТ-ёмкости, Tritan является своего рода заменой поликарбонату, но без следов Бисфенола А, для толстостенных ёмкостей многоразового применения.
В таких применениях как бутылки для детского кормления, спортивные бутылки и подобных именно Tritan вытесняет поликарбонат. Это стало возможным благодаря особым характеристикам этого полимера, которые как и поликарбонат обеспечивают контейнерам из него комбинацию отличной прозрачности, прочности и устойчивости к температурному воздействию (изделия из Tritan можно стерилизовать паром, мыть в посудомоечных машинах и т.п.).
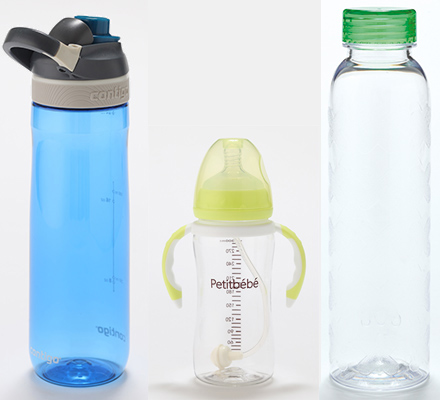
19 л бутылки для воды остаются пограничным изделием, где поликарбонат (по крайней мере на наших рынках) более распространён, но и Tritan также применяется «под соусом» меньшего вредного воздействия (нет пресловутого Бисфенола А).
По цене сырья Tritan можно отнести к той же высокой категории как и ПК, но если качественный выдувной ПК предлагают как минимум три крупных холдинга (Bayer/Covestro, Sabic и Mitsubishi) с соответствующей конкуренцией между собой, то Tritan — эксклюзивный продукт Eastman.
Основная технология для производства выдувных изделий из Tritan — инжекционно-выдувное формование с вытяжкой (ISBM). По сравнению с классическим ПЭТ для этого сополиэфира рекомендуется использовать шнеки с улучшенной характеристикой смешивания, но главной особенностью при переработке Tritan становится увеличенный объём впрыска, т.к. большинство тритановых продуктов имеют экстремально толстые стенки (в особенности спортивные бутылки, которые при вместимости 700–900 мл весят 80–100 г).
Очень часто производительность при выдуве из Tritan ограничивает именно объём впрыска станка (ограничение кол-ва гнёзд) и/или скорость пластикации (увеличение времени цикла). В этом аспекте очень хорошо подходят для данного полимера инжекционно-выдувные машины Aoki серии AL, которые комплектуются большими типоразмерами узлов впрыска и обеспечивают высокую производительность для изделий из Tritan.
ПА (Полиамид, по-английски — Polyamide, кратко PA)
Полиамид обладает великолепными химическими барьерными свойствами и может хорошо удерживать агрессивные вещества типа пестицидов, летучие соединения, топливные жидкости и/или пары. Материал перерабатывается экструзионно-выдувным формованием и чаще всего используется в многослойных (COEX) композициях вместе с полиэтиленом или (реже) полипропиленом. Причём, из-за того, что ПА не склеивается напрямую с полиолефинами в рукавной заготовке, между ними приходится предусматривать адгезивный слой, что делает структуру изделия минимум 3-х слойной.
Примечание: На международном полимерном жаргоне полиамид иногда именуют нейлоном (Nylon), поскольку именно под такой торговой маркой компании DuPont в ХХ веке данный материал прославился и получил широкое применение в различных отраслях.
Из-за высокой цены и некоторых технических ограничений (например, к полиамиду не припаивается индукционная мембрана из фольги) полимер в выдувных изделиях используют, как уже было сказано выше, вместе с полиолефинами в качестве тонкого внутреннего слоя (5–15% от массы ёмкости). Но есть случаи, когда экструзионно-выдувные изделия состоят целиком из ПА в один слой. Это несколько видов автокомпонентов так или иначе взаимодействующих с топливом: впускной коллектор, трубки, бак для паров бензина, а также сам топливный бак.
Что касается последнего, то баки для массовых автомобилей чаще всё-таки производят из COEX-композиций (об этом рассказали в статье о выдувных автокомпонентах), а 100% полиамидные — удел специализированной малотиражной техники, где больше важна стоимость и доступность экструзионно-выдувного оборудования (COEX-машины на крупногабаритные изделия — это очень дорого). Наиболее известная марка ПА для таких технических применений — Selar от всё той же DuPont.
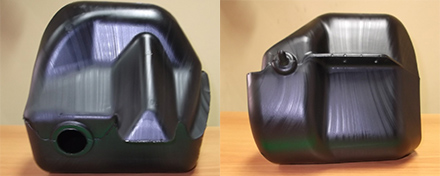
Особенности переработки полиамида экструзионно-выдувным формованием помимо обязательной тщательной просушки весьма варьируются от конкретного применения, условий и марки сырья. Теоретически для полиамида должен быть использован отличный от полиэтилена дизайн шнека, но на практике качественные выдувные марки полиамида, такие как DSM Akulon или EMS Grivory хорошо перерабатываются и в небольших по типоразмеру (до 40–50 мм диаметр) ПЭ-экструдерах (сателлитный экструдер COEX-машины). В целом по сравнению с ПЭНД полиамид требует более высоких температур и генерирует большие (по сравнению) внутренние нагрузки в экструзионной системе.
Некоторые марки полиамида перерабатываются инжекционно-выдувным формованием с вытяжкой (ISBM) и используются для производства детских бутылок для кормления, т.к. полимер полностью прозрачный и обладает достаточной термостойкостью.
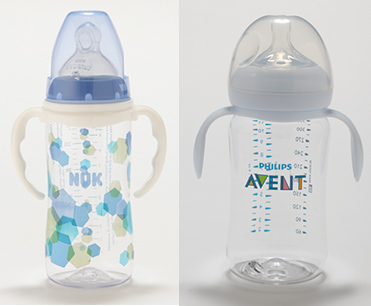
ТЭП (Термоэластопласты, они же термопластичные эластомеры, обозначаются также как ТПЭ, по-английски — Thermoplastic Elastomer, кратко TPE, TE, TPEL или TR)
ТЭП — это семейство сложных материалов, состоящих из композиций различных полимеров, которые объединены одним ключевым свойством — обладают эластичностью резины, но при этом перерабатываются как классические термопласты. Иными словами, термоэластопласт — это некая комбинация резины и пластика.
Эластомеров существует масса вариантов разного происхождения (метода получения) с разным составом и с разным набором характеристик. Некоторые из них могут перерабатываться экструзионно-выдувным способом и в этом случае используются для технических изделий, которые в процессе эксплуатации должны, по простому говоря, постоянно сжиматься и разжиматься. В отличие от резины, детали из ТЭП со временем не изнашиваются и не теряют своей упругости и эластичности, поэтому это хороший материал для соответствующих применений.
Основным примером такого применения можно назвать чехлы автомобильных амортизаторов, которые представляют из себя гофрированный цилиндр с элементами крепления. Данное изделие производят из этилен-пропиленового каучука (EPDM), эластомера на базе пропилена, который обеспечивает хорошую твёрдость в сочетании с упругостью. Некоторые известные торговые марки подобных полимеров на международном рынке: Santoprene, Alfater XL, Kopel.
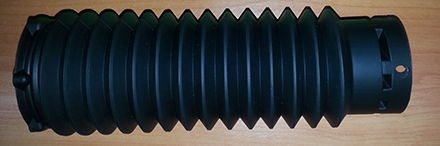
Ввиду того, что ТЭПы являются довольно мягкими полимерами, производство из них осуществляется на стандартной полиэтиленовой конфигурации экструзионно-выдувного оборудования. Есть лишь некоторые нюансы с финишной обработкой изделий (удаление облоя, вырезание технологических отверстий или обрезание фальш-элементов) — техника может отличаться от ПЭ из-за эластичности заготовки (проминается).
И совсем редкие выдувные полимеры
Буквально по паре слов скажем о ещё нескольких видах выдуваемых пластиков, которые смело можно назвать «супернишевыми» или даже экзотическими для выдувной отрасли.
ПММА (Полиметилметакрилат, он же Акрил, он же Плексиглас, по-английски — Polymethyl methacrylate, кратко PMMA или AS)
ПММА — вариация на тему поликарбоната, но проигрывающая по механической прочности и термостойкости. Материал считается более дешёвым по сравнению с ПК, но найти выдуваемые марки крайне сложно, что делает общую его доступность даже меньше.
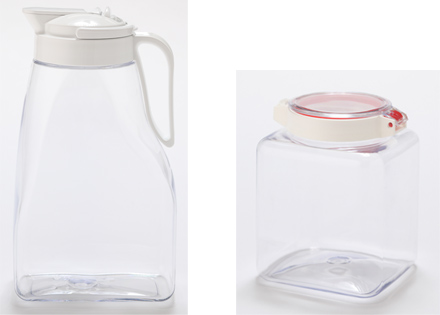
ПММА может перерабатываться инжекционно-выдувным формованием с вытяжкой (ISBM) и в этом случае используется для ёмкостей многоразового применения: графины, соусники и т.п.
ПФС (Полифениленсульфид, по-английски — Polyphenylsulfone, кратко PPSU, PSF, PES)
Изначально инженерный пластик получил некоторое применение в выдувном формовании благодаря комбинации таких свойств как прозрачность + отличная химическая стойкость + отличная температурная стойкость + устойчивость изделий к механическим нагрузкам. Может считаться альтернативой Tritan и применяется в той же группе изделий: бутылки для детского кормления и спортивные бутылки.
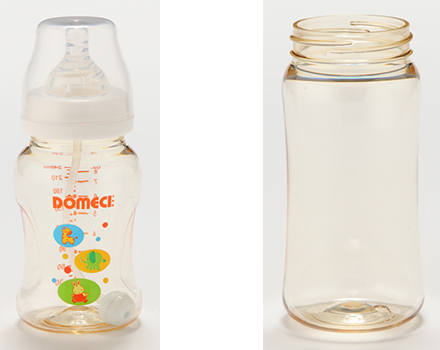
Обычно перерабатывается инжекционно-выдувным формованием с вытяжкой (ISBM), хотя концерн BASF в 2021 году запустил дополнительную марку Ultrason P 3010, которая по утверждению компании подходит и для экструзионно-выдувного формования (впрочем, непонятно для каких именно изделий её ориентировали, т.к. бутылки многоразового применения это, однозначно, вотчина технологии ISBM).
Циклоолефины (Они же же Циклоалкены, по-английски — Cyclic olefin copolymer, кратко COC или COP)
Относительно новый вид пластиков. В выдувном формовании находит некоторое применение благодаря прозрачности, термостойкости, отличным барьерным свойствам, в частности по влаге. Комбинация таких свойств востребована в химической отрасли и фармацевтике высокого уровня, в частности в контейнерах для вакцин, которые производятся из COC инжекционно-выдувным формованием с вытяжкой (ISBM).
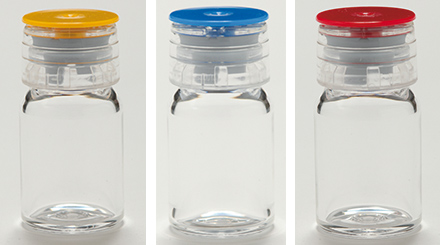
Циклоолефины могли бы заменить стекло в этих сферах (и иногда заменяют), но с учётом малой доступности и высокой цены полимера пока трудно представить себе массовое применение.
ПЭН (Полиэтиленнафталат, по-английски — Polyethylene Naphthalate, кратко PEN)
ПЭН прозрачен, как и ПЭТ, но превосходит его по теплостойкости, химической и газопроницаемости. Выглядит неплохо, почему бы этому полимеру не стать реальной альтернативой ПЭТ? Проблема в том, что ПЭН фактически производит одна компания в мире (Teijin, Япония) и его стоимость превышает 16 ЕВРО за 1 кг.
Несмотря на такие ограничения на косметическом и фармацевтическом рынке можно встретить отдельные флаконы из PEN (произведённые инжекционно-выдувным формованием с вытяжкой), но лишь для продуктов с очень высокой добавленной стоимостью.
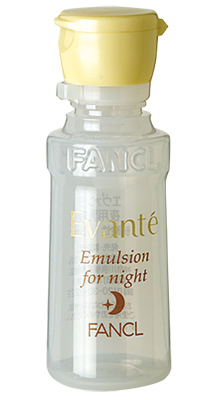
ПЛА (Полилактид, по-английски — Polylactic acid, кратко PLA)
ПЛА — биоразлагаемый полимер, получаемый из растительных источников таких как кукуруза и сахарный тростник. Всё ещё не слишком распространён на рынке выдувных изделий, однако уже доступны марки некоторых производителей, позволяющие получать бутылки и флаконы методом инжекционно-выдувного формования с вытяжкой (ISBM).
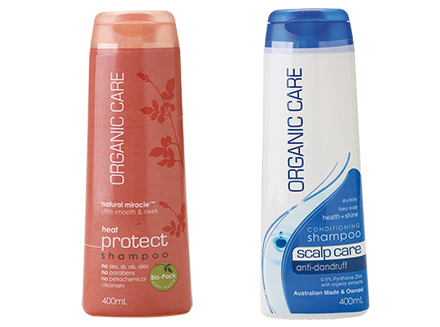
Экологические преимущества ПЛА как сырья «свободного от нефти» в каком-то смысле схлестнулись с другой эко-тенденцией о переработке тары из традиционных полимерных материалов и использовании полученного вторичного сырья. Второе на рынке на данный момент заметно больше.
***
Как кажется, в двух частях ультимативного гида мы рассказали обо всех видах полимерных материалов, которые могут быть использованы в выдувном формовании. Да, мы не упоминали, например, барьерный материал EVOH, но только по той причине, что он никогда не используется для изделия целиком, а лишь как отдельный слой в составе композиции (в отличие от того же полиамида). Если у вас остаются вопросы по упомянутым или не упомянутым в статье полимерам, то вы можете смело задавать их в комментариях.