Для выдувного формования могут быть использованы различные полимеры из довольно длинного списка. В принципе, почти все известные типы пластиков в той или иной степени, но перерабатываются или перерабатывались выдувным способом. Однако, если мы начинаем переходить от теории к практике, то оказывается, что действительно актуальными полимерными материалами для выдува являются всего несколько, а остальные или имеют нишевое применение или практически «вымерли» на сегодняшний день.
Наш гид расскажет об особенностях применения и переработки всех основных выдувных полимеров. Чем более актуальным является конкретный материал тем подробнее о нём. Порядок — в соответствии с общепринятой международной нумерацией маркировки пластиков.
№1 — ПЭТ (Полиэтилентерефталат, обозначается также как ПЭТФ, по-английски — Polyethylene terephthalate, кратко PET или PETE)
Главная особенность ПЭТ (и она же, главное рыночное преимущество) — чистая прозрачность. Выдувная тара из ПЭТ столь же прозрачна как стекло, поэтому почти всё, что исторически упаковано (упаковывалось и упаковывается) в такой классический бутылочно-баночный материал как стекло можно с теми или иными нюансами перевести в ПЭТ. Этот материал по сравнению со стеклом как минимум:
- Легче
- Не бьётся (по крайней мере так легко)
- Дешевле
Благодаря громадной популярности и массовости ПЭТ стал очень широко доступным, конкурентным, а следовательно недорогим материалом. Ситуация меняется в зависимости от конкретного рынка и текущей конъюнктуры, но в целом на сегодняшний день ПЭТ чаще всего оказывается самым дешёвым выдуваемым полимером.
ПЭТ / Применения
С количественной точки зрения наиболее известное применение ПЭТ — бутылки для напитков. Для розлива обычной воды никаких физико-химических свойств полимера не требуется, поэтому прозрачность становится основным требованием и маркетинговой причиной для выбора ПЭТ. Материал имеет низкую газопроницаемость (намного лучшую по сравнению с любым другим полимером), в частности, по углекислому газу, поэтому для любых газированных напитков ПЭТ также обычно является первым выбором.
ПЭТ применяется также для упаковки:
- Соков и других «вкусовых» напитков (при условии, что продукт в момент розлива имеет температуру не более 50–55 градусов по Цельсию)
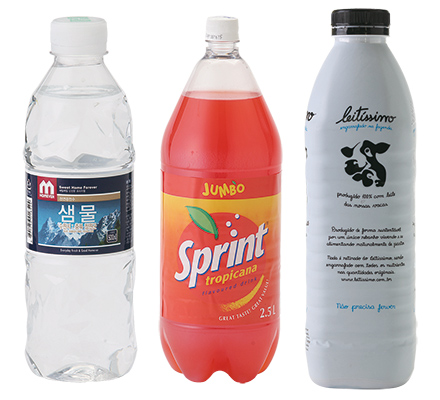
- Спиртосодержащих продуктов, это могут быть и пищевые и непищевые жидкости, например, огромный спектр медицинских средств (ПЭТ имеет очень хорошие барьерные свойства по спиртам, поэтому для хранения спиртосодержащих не отличается от стекла)
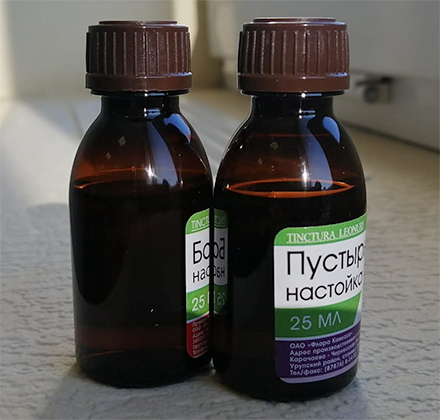
- Растительных масел (ПЭТ, во-первых, нейтрален к ним, во-вторых, обеспечивает подходящий внешний вид товара)
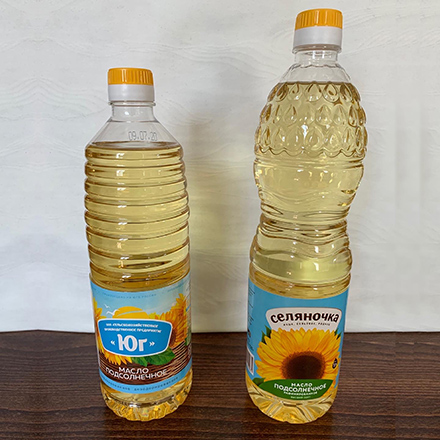
- Молока (за исключением длительного хранения, например, более 15–21 дней; зависит в т.ч. и от конкретных условий розлива)
- Кисломолочных продуктов
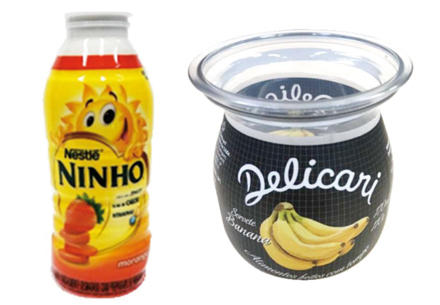
- Соусов и майонезов (благодаря неплохой барьерности по кислороду)
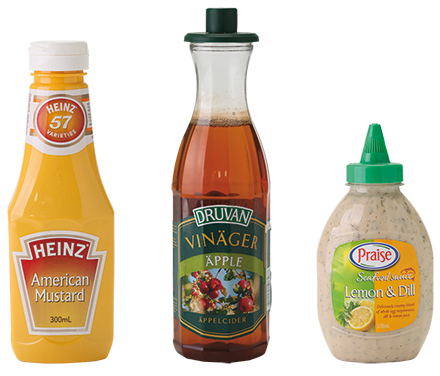
- Косметических средств
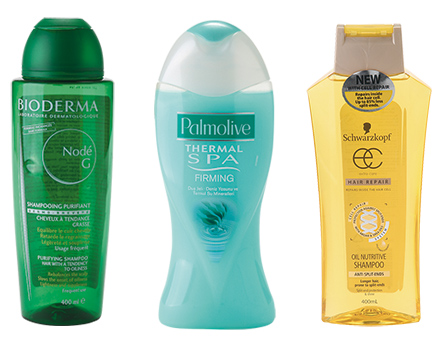
- Бытовой химии (за исключением щелочей, гипохлоритов и других агрессивных средств с высоким показателем pH)
- Различной химии (например, некоторые виды кислот и растворителей)
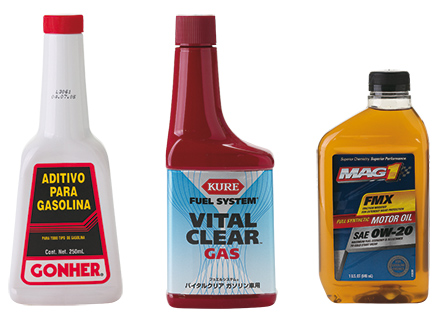
- БАД, витаминов и различных лекарственных средств (за исключением гигроскопичных или не нейтральных к ПЭТ)
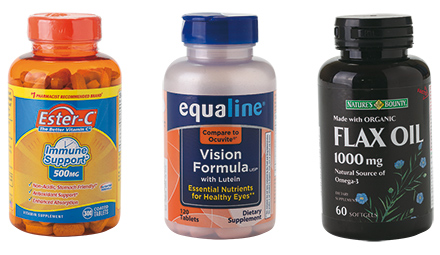
- Различных сыпучих продуктов (например, соль, сахар, крупы)
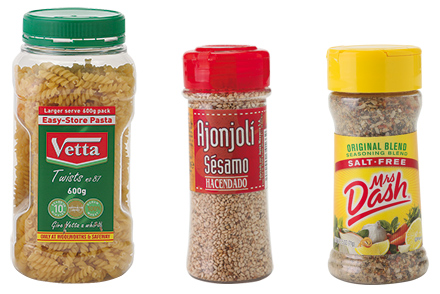
Кроме упаковки из ПЭТ производят выдувом банки и контейнеры с широким горлом хозяйственного назначения, а также другие выдувные изделия более специального применения.
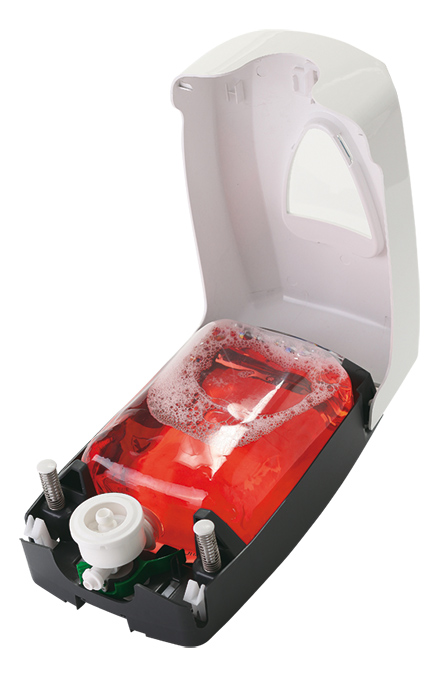
ПЭТ / Переработка
Выдувную тару из ПЭТ можно производить следующими технологиями:
- Инжекционно-выдувное формование с вытяжкой (также известное как моностадийная технология или ISBM)
- 2-стадийное выдувное формование (литьё заготовки-преформы на термопластавтомате, затем на отдельной машине её нагрев и раздув)
И в том и в другом случае сначала из ПЭТ формируется твёрдая заготовка с зафиксированной горловой частью, а затем она раздувается до конечной формы изделия. По-другому (например, экструзионно-выдувным способом — через эластичный рукав-заготовку) ПЭТ не перерабатывается.
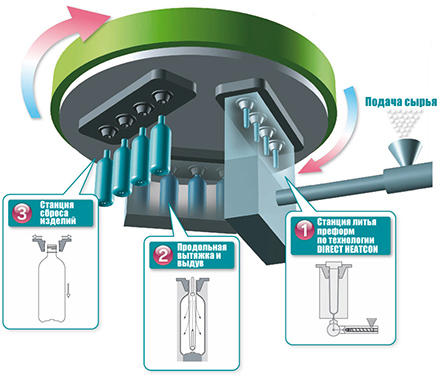
Существует очень небольшой сектор производства маленьких ёмкостей из ПЭТ на горизонтальных инжекционно-выдувных машинах без вытяжки (IBM), но в связи с очень большой капризностью техпроцесса, ограничениями по видам возможных флаконов, такой метод едва ли жив и сегодня фактически замещён ISBM.
ПЭТ — довольно термочувствительный материал и перерабатывается при относительно высоких температурах (250–300 °C). Небольшие изменения (или отклонения) технологических режимов литья (и/или повторного разогрева) оказывают значительное влияние на свойства преформы (заготовки), что напрямую влияет и на конечную ёмкость.
ПЭТ очень хорошо растягивается из горячей преформы при выдуве сжатым воздухом и легко принимает коэффициенты раздува (разница в размере заготовки и размере конечного флакона/бутылки) в несколько раз, при этом после окончания выдува мгновенно остывая. В процессе раздува заготовки даже те её фрагменты, которые уже коснулись стенок выдувной прессформы, всё равно могут продолжать растягиваться под воздействием сжатого воздуха «облепляя» всё внутренне пространство.
ПЭТ имеет наибольшую плотность по сравнению с другими видами выдуваемого сырья (около 1,4), а тара получает характерную жёсткость и может относительно неплохо держать форму даже при очень маленьких толщинах стенки (например, менее 0,2 мм) при наличии в конструкции бутылки рёбер жёсткости. Вкупе с хорошей растягиваемостью это позволяет из одной и той же преформы с одним весом выдувать самые разные изделия прилично различающегося объёма.
ПЭТ — гигроскопичный материал и перед попаданием в узел впрыска литьевой машины должен быть тщательно просушен. Для этой цели используются т.н. влагоустранители, т.е. сушилки, обеспечивающие циркуляцию в замкнутом контуре воздуха через силикагельные сита, забирающие на себя извлечённую из гранул сырья влагу. С помощью таких устройств можно достичь искомой точки росы материала (как правило, -45–55 °C) для качественной переработки.
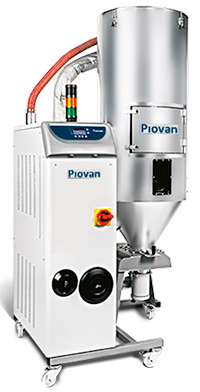
Что касается, различий (преимуществ / недостатков) между моностадийным и 2-стадийным принципом изготовления ПЭТ-ёмкостей, то на эту тему сломано немало копий, и в т.ч. об этом мы говорили во время нашего вебинара о ISBM-технологии, запись которого можно посмотреть здесь.
ПЭТ / Минусы
Главный недостаток ПЭТ, пожалуй, — ограничение по температуре эксплуатации полученных ёмкостей. По теоретическим характеристикам материал начинает размягчаться при температуре около 70 °C, но на практике налив в ПЭТ-тару или обработка продукта в бутылке при более 55 градусах уже приводит к возникновению деформаций, которые в зависимости от конкретных условий могут стать критическими для проекта.
Существуют различные технологические ухищрения, которые позволяют поднимать температурный барьер ПЭТ-тары (специальное термостатирование при выдуве и/или специальная конструкция изделия и/или специальные марки ПЭТ и/или иные решения), но все они так или иначе удорожают процесс, лишая сырьё одного из основных преимуществ — дешевизны.
Ещё из недостатков ПЭТ — невозможность производства толстостенных изделий с высокой добавленной стоимостью. При толщинах стенки конечной ёмкости, как правило, 2 мм и более полимер при формовании начинает кристаллизоваться, что оставляет белёсые полосы, разводы и целые секции на изделии, уничтожая его товарный вид.
ПЭТГ / PET-G и другие родственники ПЭТ
Помимо стандартного т.н. «бутылочного» ПЭТ есть его модифицированные версии, призванные нивелировать те или иные слабости материала. В основном это касается температурной стойкости и излишней кристаллизации (появления белёсых разводов). Некоторые из таких вариаций ПЭТ выделяют как отдельный вид сырья, например, так можно сказать о материале ПЭТГ (по-английски PETG / PET-G) — это ПЭТ, модифицированный гликолем и получивший соответствующее полное название Полиэтилентерефталатгликоль (Polyethylene terephthalate glycol).
ПЭТГ имеет «нулевую» кристаллизацию, т.е. изделия из него с любой толщиной стенки в любых режимах литья не будут иметь белёсых фрагментов — это открывает возможности для изготовления различного рода премиальных косметических баночек, как правило, моностадийной технологией ISBM, а также иных толстостенных невыдувных изделий.
Другая (для многих даже более известная) особенность ПЭТГ — возможность его переработки экструзионно-выдувным формованием (из ПЭТГ, в отличие от ПЭТ, можно получить эластичную трубчатую заготовку из головки с непрерывной экструзией). Но, поскольку материал ПЭТГ дорогостоящий (обычно около в 2-3 раза дороже стандартного ПЭТ), широкого применения в экструзионно-выдувном секторе он не имеет и используется в основном для небольших косметических флаконов с малыми тиражами выпуска на дизайн (там где производить ISBM-оснастку слишком дорого ввиду маленькой программы выпуска конкретного вида флакона).
Пример из практики автора. Флакон для туши — вытянутое и очень узкое изделие как по диаметру тела так и по диаметру горловины (которая обычно составляет буквально несколько миллиметров). Наилучшей технологией для его изготовления является ISBM, но в бизнес-реальности (по крайней мере наших рынков) из-за большого количества разных дизайнов флаконов для туши, каждый из которых зачастую ещё и имеет свою конструкцию горловины, получается, что стоимость ISBM-оснастки не оправдывает тираж выпуска. Поэтому в игру вступает экструзионно-выдувное формование.
Прозрачность для флаконов этого применения нужна довольно редко, поэтому, казалось бы, для производства следует просто использовать один из полиолефинов (полиэтилен или полипропилен). Рукав для формирования столь узкого изделия также делается максимально узким, но, при использовании полиолефина, в момент сжатия трубчатой заготовки прессформой она складывается и расширяется таким образом, что уже начинает заступать по ширине как за пределы горловины, так и за пределы основного корпуса флакона. Это делает нормальное производство невозможным.
На помощь приходит ПЭТГ. Рукав из этого материала гораздо более «жидкий» (стремится течь вниз как вода) и при защипывании прессформой имеет тенденцию оставаться круглым и не расширятся, что позволяет производить очень узкие изделия без облоя по бокам.
При переработке ПЭТГ на экструзионно-выдувной машине есть особенности по сравнению с традиционными для этой технологии полиолефинами. Во-первых, требуется тщательная просушка (как и при литье обычного ПЭТ), во-вторых, материал термочувствительный, поэтому геометрия шнека и экструзионной головки отличается от полиэтиленовой, в-третьих, для пережатия кромки необходимо в два раза больше усилия смыкания по сравнению с полиэтиленом.
ПЭТГ — нишевый материал узкого применения, но мы говорим о нём в этом разделе, т.к. чаще всего ёмкости из ПЭТГ маркируют цифрой «1» (также как ПЭТ). Есть и другие вариации на эту же тему, например, семейство сополиэфиров (copolyester) ПЭТ от компании Eastman (и некоторых других менее известных производителей), которые позволяют производить экструзионно-выдувным формованием крупные кристально прозрачные ёмкости с ручкой. Такие бутылки выглядят очень элегантно и выделяются на полке, но стоить помнить и об их стоимости. К сожалению, сополиэфиры ещё дороже ПЭТГ.
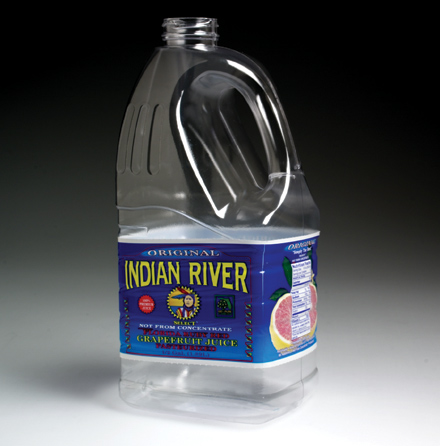
Кстати, материал маркируют на контейнерах из сополифиров зачастую как просто PET или PETE, поэтому разницу со стандартным ПЭТ можно подтвердить только технологией изготовления (ёмкость из стандартного ПЭТ всегда имеет точку впрыска от литья преформы).
Для производства толстостенных банок и флаконов методом ISBM помимо ПЭТГ есть и другие типы пластиков такие как PCTA или PCTG — всех их иногда условно объединяют в одну группу и именуют «стеклополимерами» (хотя ничего общего со стеклом с физико-химической точки зрения они не имеют, а лишь имитируют его по внешнему виду и органолептике).
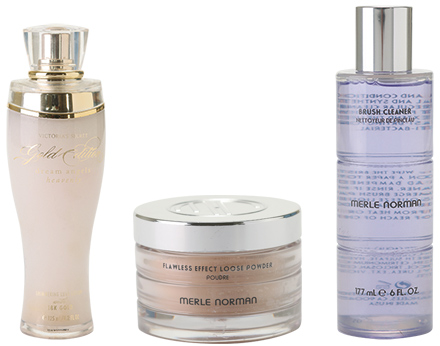
Ещё одним весьма известным сополиэфиром ПЭТ стал материал от Eastman под торговой маркой Tritan. К нему мы вернёмся в следующих разделах, поскольку Тритан обычно обозначают уже не под цифрой «1».
№2 – ПЭНД (Полиэтилен низкого давления, он же полиэтилен высокой плотности, обозначается ПЭНД или ПНД или ПЭВП, по-английски – High Density Polyethylene, кратко HDPE или PE-HD)
Если смотреть в общем на отрасль переработки пластмасс (а не только на выдув), то полиэтилен (в совокупности все его виды) — самый «классический» и распространённый полимер на планете. В выдувном формовании полиэтилен, а точнее его основной подвид ПЭНД (полиэтилен низкого давления), уверенно входит в большую двойку основных перерабатываемых типов сырья, соседствуя там с ПЭТ. Некоторые новички отрасли даже путают эти два материала, ведь названия обоих начинаются со слов «полиэтилен», но на самом деле ПЭНД и ПЭТ кроме общей части в названии не имеют больше ничего общего. И по внешнему виду, и по свойствам и по переработке отличия у них кардинальные.
ПЭНД / Применения
Как и из ПЭТ, из ПЭНД производят выдувную тару для широкого круга отраслей и перечислять примеры можно бесконечно (стоит посмотреть список применений ПЭТ выше), но, поскольку свойства материалов отличаются, то у применения ПЭНД есть свои выраженные аспекты, которые мы и выделим:
Отсутствие прозрачности. Естественный цвет ПЭНД — серый и практически не прозрачный (можно видеть лишь уровень, но не цвет содержимого), а поверхность матовая (в то время как ПЭТ — сильный глянец). Поэтому для видов продукции, где уже по маркетинговым соображениям нужна полная прозрачность ПЭНД автоматически не подходит. Среди таких применений можно выделить: почти весь рынок воды и газированных напитков, растительных масел, алкогольных напитков из тех, что фасуются в пластиковую тару. Также это отдельные конкретные продукты из других отраслей, где на рынке уже устоялся образ полностью прозрачной упаковки.
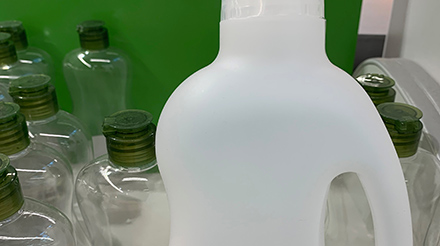
С другой стороны, для непрозрачной тары, окрашенной в какой-то конкретный сплошной цвет ПЭНД по тем же самым маркетинговым соображениям чаще подходит больше, чем ПЭТ, т.к. на полностью непрозрачном окрашенном флаконе или банке матовость ПЭНД смотрится благороднее, чем глянец ПЭТ. Поэтому, например, огромное множество цветных флаконов для шампуней или гелей для душа производятся именно из ПЭНД.
Возможность переработки экструзионно-выдувным формованием. О способах переработки ПЭНД ещё обсудим дальше, но главная особенность, т.е. возможность переработки экструзионно-выдувным способом, сильно влияет на сферу применения материала. Экструзионно-выдувная ёмкость может иметь более сложную геометрию по сравнению с выдувом через преформу (как у ПЭТ) и в первую очередь — это возможность формирования полноценной ручки. Таким образом, практически весь рынок флаконов, бутылок и канистр с ручками по умолчанию забирает себе ПЭНД (оставшаяся небольшая часть этого сегмента остаётся полипропилену и некоторым нишевым материалам).
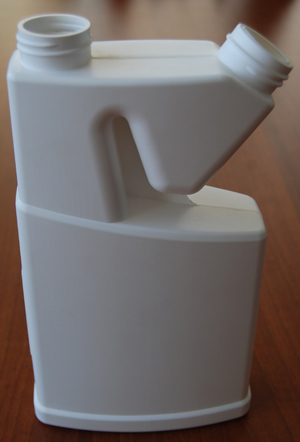
Кроме того, экструзионно-выдувное формование позволяет широко использовать ПЭНД и в неупаковочном секторе: для автокомпонентов и различных технических изделий (игрушки, хозяйственные предметы и т.п.).
Интересно, что благодаря тому, что эффективную крупногабаритную промышленную тару (канистры) технологически можно производить только из ПЭНД, то даже те виды содержимого, которые с химической точки зрения лучше хранятся в ПЭТ, всё равно фасуют в ПЭНД. К такой продукции можно отнести растительные масла или спирт/спиртосодержащие — при мелкой (розничной) фасовке используется ПЭТ, а для промышленной транспортировки — ПЭНД.
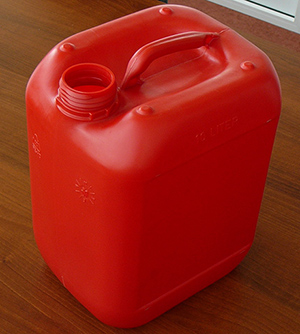
Температурная стойкость. Тара из ПЭНД имеет довольно уникальную комбинацию температурной стойкости в обе стороны: отлично переносит мороз и также имеет хороший верхний порог по нагреву.
По спецификациям размягчение полиэтилена начинается примерно после 100–105 градусов, но в зависимости от конкретных условий тара может вести себя по-разному. Выдержит ёмкость или не выдержит предъявляемые требования при температурном воздействии сильно зависит от следующих факторов (как по отдельности так и в комбинации):
- Дизайн ёмкости
- Содержимое ёмкости и создаваемое им самим при температурном воздействии избыточное давление или вакуум
- Длительность и профиль температурного воздействия
- Внешняя среда вокруг ёмкости в момент возникновения температурного воздействия (местонахождение, например, в каких-то захватах; пар, избыточное давление и т.д.)
- Строгость самих требований (например, в каких-то условиях у бутылки могут немного вдавиться внутрь стенки, в некоторых случаях — это не проблема, в некоторых — не допускается).
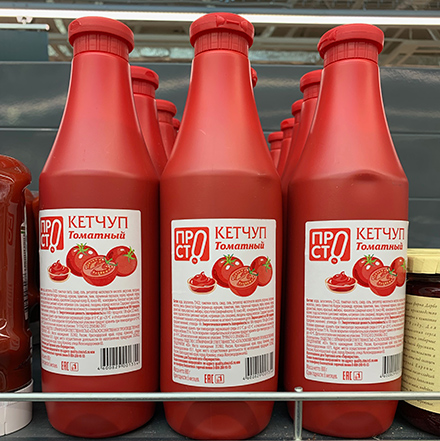
Пример из практики автора. Во второй половине 00-х мы запускали проект, где было необходимо обеспечить для тонкостенной (40 г) круглой молочной бутылки 1 л из ПЭНД автоклавирование при температуре 125 градусов на протяжении 1 часа (стерилизация молока для продления срока годности). Задача звучит невыполнимой (учитывая характеристики размягчения ПЭНД), однако на рынке существовали примеры успешной реализации подобного проекта, поэтому было понятно, что результат в теории достижим. На практике каждый раз получалось, что дно после автоклава выпирает так, что бутылка становится «неваляшкой».
После длительных технологических изысканий (переходящих в мучения) был, наконец, найден рецепт успеха — он состоял в определённом профиле донной части бутылки. По сути дно должно было быть нарочито вогнуто внутрь экстремально сильно (извлечение из прессформы было возможно только благодаря тонкой стенке и сглаженным углам). После автоклавирования дно имело тенденцию вылезти наружу, но благодаря изначально заложенному в конструкцию очень сильному поднутрению даже после такой деформации бутылка сохраняла устойчивость.
В этом случае температурное воздействие превышало стойкость тары и вызывало деформацию, но благодаря определённой специально подобранной конструкции изделия деформация оказалась контролируемой и не приводила к браку.
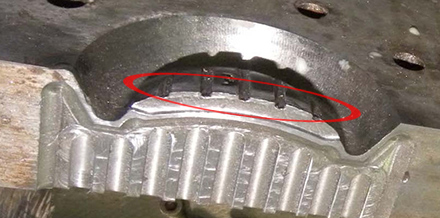
Стойкость к агрессивной химии. Тара из ПЭНД хорошо подходит для хранения и транспортировки щелочей, гипохлоритов и других агрессивных средств с высоким показателем pH — здесь прослеживается ещё одно большое отличие от ПЭТ, который для такого содержимого не пригоден.
Фактически это огромная часть рынка бытовой химии, а также химических средств иных назначений. В сочетании с другими свойствами ПЭНД о которых говорилось выше (возможность производства канистр с ручками и морозостойкость) — это делает ПЭНД основным полимером для производства промышленной упаковки в химической отрасли.
Барьер для влаги. ПЭНД обладает одной из лучших среди всех материалов (и уж точно по сравнению с ПЭТ) паропроницаемостью. Проще говоря, тара из ПЭНД не позволяет проходить влаге сквозь стенки флакона и тем самым становится лучшим видом пластиковой упаковки для гигроскопичных продуктов (сюда относятся многие медикаменты в капсулах и таблетках, многие виды БАД и другие продукты).
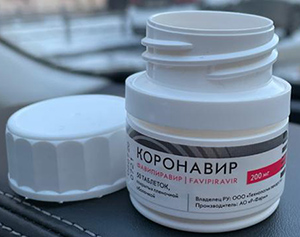
Соответствующий параметр называется MVTR (moisture vapor transmission rate) и специально измеряется / проверяется / отслеживается фармацевтическими компаниями и их поставщиками упаковки при выборе тары для соответствующих препаратов.
Многослойная (COEX) тара. Опять же благодаря возможности переработки экструзионно-выдувным формованием для ёмкостей с применением ПЭНД становится относительно доступной многослойность, которая в свою очередь улучшает барьерные свойства или в некоторых случаях снижает себестоимость. ПЭТ, с учётом переработки через литьё преформы, тоже имеет некоторые возможности по формированию многослойной заготовки (например, с добавлением кислородного барьера из EVOH), но это сильно технически и экономически затруднено по сравнению с экструзионно-выдувным формованием (нужно уж очень дорогое и редкое специализированное оборудование возможности которого ограничены).

ПЭНД / Переработка
Выдувную тару из ПЭНД можно производить следующими технологиями:
- Экструзионно-выдувное формование
- Инжекционно-выдувное формование (также известное как горизонтальное инжекционно-выдувной формование без вытяжки или IBM)
- Инжекционно-выдувное формование с вытяжкой (также известное как моностадийная технология или ISBM)
ПЭНД является, пожалуй, наименее капризным из выдуваемых полимерных материалов, однако и у этого сырья есть свои особенности и ограничения.
В экструдере ПЭНД гомогенизируется практически любым типом шнека при рабочих температурах в широком окне от примерно 160 до 240 градусов (но чаще всего всё-таки в диапазоне 180–210 градусов). В современных экструзионно-выдувных машинах для хорошей пластикации используются шнеки с большими сдвиговыми усилиями и, как правило, смешивающими зонами (поскольку экструзионно-выдувной процесс всегда подразумевает добавление в первичный материал измельчённого облоя и обычно также красителя).
ПЭНД — термостабильный полимер и для трансформации расплава в трубчатую заготовку подходят все типы головок непрерывной экструзии: пинольная, торпедная, 2-уровневная пинольная или аккумуляторные (накопительные) головки для изделий весом более 2,5–3 кг. Подробнее о различных типах головок экструзионно-выдувных машин мы рассказывали во время вебинара, ссылку на запись которого можно получить здесь.
Экструзионно-выдувные прессформы для ПЭНД изделий должны иметь матовую шагреневую поверхность, получаемую после пескоструйной обработки. Охлаждение можно осуществлять водой низкой температуры (7–8 град.) — так обеспечивается наиболее короткий цикл, но в некоторых случаях (при высокой влажности в цехе и/или неэффективно сделанных каналах охлаждения) температуру воды приходится повышать.
Метод инжекционно-выдувного формования, когда выдув осуществляется не из мягкой рукавной заготовки, а из отлитой под давлением преформы со сформированной горловиной, также используют при переработке ПЭНД, но есть ограничения. Технология подходит для формования относительно небольших ёмкостей, и обычно флаконы более 150–200 мл уже вызывают проблемы, во-первых, с точки зрения управления и поддержания радиальной разнотолщинности, во-вторых, из-за ограниченности количества гнёзд для больших изделий в типовых IBM-станках. Ещё большие трудности вызывает производство флаконов с экстремально овальным сечением и других отдалённых от круга форм.
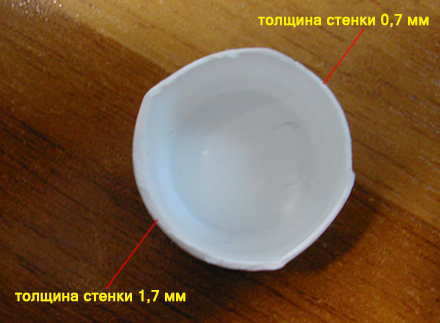
Более совершенная по сравнению с IBM технология инжекционно-выдувного формования с вытяжкой (ISBM), о преимуществах которой говорили на соответствующем вебинаре, исторически не очень хорошо подходила для переработки ПЭНД. ISBM предполагает, что преформа будет вытягиваться в продольном направлении и в стороны довольно сильно (в отличие от IBM, где коэффициенты раздува небольшие), а ПЭНД (по сравнению с тем же ПЭТ) совсем не гибок при растягивании из твёрдой заготовки. После литья ПЭНД-преформа мгновенно усаживается и не поддаётся дальнейшему раздуву, поэтому ПЭНД, конечно, иногда на ISBM-машинах перерабатывали и много лет назад, но только в режиме сверхразогретых прессформ (выше 90 градусов), что поднимало время цикла «до небес» и делало процесс неконкурентоспособным.
Настоящий прорыв в переработке ПЭНД методом ISBM совершила компания Aoki в конце 2010-х годов – японскому производителю удалось нащупать технологию производства изделий при нормально охлаждаемых холодной водой (около 15 град) прессформах. Найти работающую методику, среди прочего, помогло отсутствие на машинах Aoki промежуточной станции кондиционирования между станциями литья и выдува. В итоге был значительно расширен спектр применений ПЭНД в инжекционно-выдувном формовании с вытяжкой; сейчас речь идёт о возможности изготовления с коротким циклом ёмкостей как минимум до 1,5 л с коэффициентами раздува до 2–2,5.
Производство бутылки из ПЭНД на инжекционно-выдувной машине Aoki |
В 2020 году была успешно протестирована (и показала себя полностью пригодной для применения) на оборудовании Aoki как минимум одна марка ПЭНД российского производства (завода СИБУР ЗСНХ), в конце 2021 года планируются испытания двух других.
***
В первой части гида мы поговорили о «большой двойке» выдувных полимеров (ПЭТ и ПЭНД). Материалам более узкого назначения (ПП, ПВХ, ПК и другим) мы посвятим вторую часть, которая будет опубликована позднее.
Отлично!
Добрый день. Подскажите, при розливе в бутылку ПНД горячего продукта(85-95градусов), нет ли рисков миграции веществ из бутылки в продукт?
Здравствуйте, Вера
В бутылке нет никаких «веществ» — это обычный полиэтилен. Он так просто никуда не проникает. «Вещества» могут быть в самом содержимом, но, чтобы они проникли именно в полиэтилен — это должны быть довольно специальные (редкие) компоненты с особыми химическими свойствами. Проблемой является не взаимная миграция между упаковочным материалом и содержимым, а прохождение через стенки упаковки (тары) газов, лучей, влаги и т.п. Причём в оба направления (из тары во внешнюю среду и из внешней среды в тару).
Что касается «горячести» содержимого, то это не влияет на миграцию или барьерные свойства тары. Однако, это создаёт вакуум в бутылке после остывания продукта. Этот вакуум имеет тенденцию деформировать бутылку. Об этом рассказано в статье о критериях качества тары.